Remember Terran 1, Relativity Space’s rocket that recently launched from Cape Canaveral Space Force Station in Florida? The rocket made a real splash as it is the first one that is entirely made from 3D printed parts – measuring 100 feet tall and 7.5 feet wide.
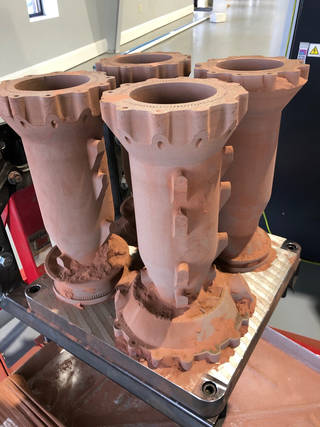
A behind-the-scenes look at the manufacturing process and other key specifications reveals interesting info about those tiny ingredients that enabled Terran 1 to lit up the night sky on March 23rd, 2023. It turns out that one of these ingredients is an innovative copper alloy from NASA that helped the rocket experience temperatures approaching 6,000 degrees Fahrenheit (3315.56 °C).
Created at NASA’s Glenn Research Center in Cleveland under the agency’s Game Changing Development program, this family of copper-based alloys known as Glenn Research Copper, or GRCop, are designed for use in combustion chambers of high performance rocket engines.
A combination of copper, chromium, and niobium, GRCop is optimized for high strength, high thermal conductivity, high creep resistance – which allows more stress and strain in high temperature applications – and good low cycle fatigue – which prevents material failures –above 900 degrees Farenheit. They tolerate temperatures up to 40% higher than traditional copper alloys, which leads to higher performance components and reusability.
The story behind the development of GRCop
In the late 1980s, NASA wanted to develop an engine for manuvering spacecraft in low-Earth orbit that could withstand multiple firings. Rocket engines encounter complex challenges in design and environments in which they operate, including multiple startups and shutdowns that create a cycle of wear and tear on critical components.
Dr. David Ellis developed the GRCop family of alloys as a NASA-supported graduate student during the space shuttle era. He continued to mature the alloys and their applications throughout his career.
“At the time, Space Shuttle Main Engine combustion chamber liners were typically replaced after one to five missions,” explained Ellis. “Our research was able to show that GRCop-84 would easily meet the goal of 100 missions between maintenance service and 500 missions of engine life.”
Throughout years of alloy development, Ellis and his team worked with multiple projects and programs, like NASA’s Rapid Analysis and Manufacturing Propulsion Technology (RAMPT), to advance different versions of GRCop alloys. The most recent iteration, named GRCop-42, uses a variety of additive manufacturing methods to create single-piece and multi-material combustion chambers and thrust chamber assemblies for rocket engines. These processes improved the performance, while significantly reducing weight and costs of thrust chamber components.
The processing of GRCop by laser powder bed fusion & DED
NASA found out that laser powder bed fusion and directed energy deposition are two approaches that can be used to build GRCop parts for many aerospace applications, such as the Terran 1 rocket engines.
“Development projects, like RAMPT, allow advancement of new alloys and processes for use by commercial space, industry, and academia,” said Paul Gradl, principal engineer at NASA’s Marshall Space Flight Center in Huntsville, Alabama. “NASA takes on the development risk and matures the process from early material and process concepts through certification. This infusion of GRCop-42 alloys into commercial space is another great example of how NASA-led innovations advance industry capabilities and contribute to America’s growing space economy.”
Remember, you can post job opportunities in the AM Industry on 3D ADEPT Media free of charge or look for a job via our job board. Make sure to follow us on our social networks and subscribe to our weekly newsletter : Facebook, Twitter, LinkedIn & Instagram ! If you want to be featured in the next issue of our digital magazine or if you hear a story that needs to be heard, make sure to send it to contact@3dadept.com