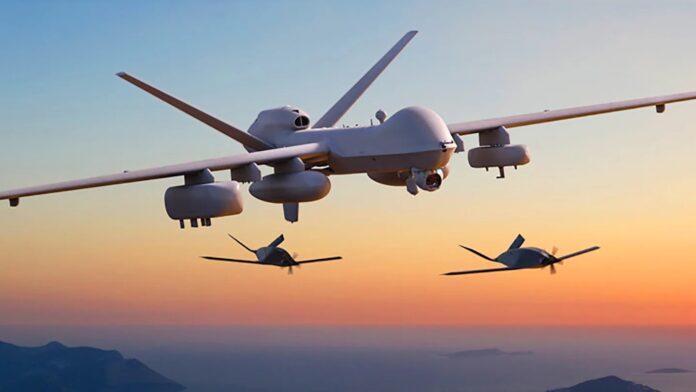
Avec des millions de dollars déjà économisés en outillage, General Atomics Aeronautical Systems, Inc. (GA-ASI) partage les leçons apprises de son aventure dans la FA industrielle. Un exemple significatif de leur histoire est lié à la production d’une fixation de laminoir réalisée en collaboration avec Thermwood, qui a permis de réaliser 50 000 dollars d’économies.
Lorsque vous êtes un journaliste spécialisé dans l’industrie de la fabrication additive, l’une des étapes importantes que vous êtes impatient de voir chez les utilisateurs est l’installation d’une pièce de production dans leurs opérations. À ce moment-là, vous vous dites : « Nous atteignons un point de basculement. Nous y arrivons, lentement mais sûrement. C’est un rêve qui devient réalité ». Nous avons assisté à ce moment pour General Atomics Aeronautical Systems, Inc. (GA-ASI) en 2019, lorsque l’entreprise a fait voler avec succès son premier composant métallique imprimé en 3D ; une entrée NACA en titane Ti6AI4V sur un avion piloté à distance (APR) MQ-9B Sky Guardian. Même s’il s’agit de l’une des premières étapes dont nous ayons été témoins, il s’avère que les activités de l’entreprise en matière de FA ont débuté il y a près de dix ans et il a fallu une conversation avec Steve Fournier pour comprendre tout le cheminement qui y a mené.
Si vous êtes nouveau dans cet espace, sachez que General Atomics (GA) est une entreprise de défense et de technologies diversifiées qui développe une large gamme de produits tels que des systèmes énergétiques et des systèmes d’avions sans pilote. Même si la FA est utilisée dans plusieurs divisions de FA, l’adoption de la technologie est largement encouragée par GA-ASI. GA-ASI est un maître d’œuvre du ministère américain de la défense (DoD), et est surtout connu pour la conception et la fabrication de véhicules aériens sans pilote et de systèmes radar. Steve Fournier, qui partage aujourd’hui l’expérience de l’entreprise en matière de FA, est directeur principal du centre d’excellence de GA-ASI pour la conception et la fabrication additive.
L’aventure de GA-ASI dans le domaine a commencé au début des années 2010, lorsque l’entreprise a décidé d’explorer l’utilisation de la FA pour les applications RPA. Avant d’investir dans une technologie de FA spécifique, les équipes d’ingénieurs de l’entreprise ont travaillé sur différents projets menés en collaboration avec des fabricants de machines et des services de bureau. De cette façon, ils ont pu en apprendre davantage sur les capacités de chaque technologie et de chaque matériau avant de les intégrer dans leur entreprise. Ils ont embarqué leur premier système de FA en 2011, une technologie Polyjet de Stratasys. Au fur et à mesure que sa courbe d’apprentissage progressait, ils ont enrichi leur portefeuille d’applications de développement avec un large éventail de procédés de FA qui ont suivi une progression typique en passant par les technologies FDM, SLS puis de FA métal.
Utilisant aujourd’hui plus de sept modalités différentes de processus de FA pour de multiples applications, GA-ASI continue d’investir dans plusieurs éléments essentiels à la croissance de la FA pour servir les produits et les clients de GA-ASI. Plus précisément, GA-ASI a investi beaucoup de ressources dans les infrastructures des installations, dans une équipe d’experts en la matière (PME) en pleine croissance, dans les équipements de FA ainsi que dans la R&D afin de réduire les risques à plusieurs niveaux liés aux matériaux, aux processus et aux applications.
Cela signifie, par exemple, qu’à des fins de prototypage rapide (hors vol), GA-ASI a développé de multiples ressources en interne, y compris le groupe de FA qui soutient l’ingénierie et exploite la plupart des technologies de FA, tandis que pour les opérations de fabrication des pièces de développement et de production de produits prêts pour le vol, FDM, SLS, métal-LPBF, DED-W, BJT et LSAM/BAAM seront plus indiqués. Il va sans dire que ces technologies sont complétées par des capacités de conception technique (DfAM), des équipements de post-traitement, des infrastructures de conditionnement et de test des matériaux, d’inspection ou de métrologie.
« Avec près de 7 000+ pièces imprimées en 3D par an, nous avons plus de 320 UGS différentes qui volent aujourd’hui sur plusieurs de nos plateformes d’avions, ce qui représente plus de 300 000 heures de vol cumulées. Cela représente un mélange de pièces en polymère, en composite et en métal. Le marché des APR militaires, avec son modèle à forte mixité et à faible volume, est un secteur parfait de l’industrie aéronautique pour introduire la FA. Dès 2011, nous avons commencé à mettre en place nos infrastructures et à introduire nos premières imprimantes, etc. À l’époque, il s’agissait principalement d’applications de prototypage pour nous aider à explorer les matériaux et les domaines potentiels de ses applications sur nos produits. En 2016/2017, les dirigeants de GA-ASI ont reconnu la valeur et la nécessité de constituer une équipe d’experts en la matière pour chaque procédé de FA, et en 2018, un département officiel a été créé. Nous avons commencé avec seulement quatre personnes, et maintenant, nous avons 14 personnes dédiées aux technologies de FA. L’un de nos principaux domaines d’intervention était de développer la structure de notre feuille de route stratégique composée d’un écosystème de technologies de FA pour nous aider à passer du prototypage à une opération prête pour la production et aider à piloter sa mise en œuvre dans toute l’organisation afin d’aller chercher de multiples applications. Le procédé LSAM de Thermwood n’est qu’une des nombreuses technologies qui nous permet d’atteindre cet objectif », raconte Fournier.
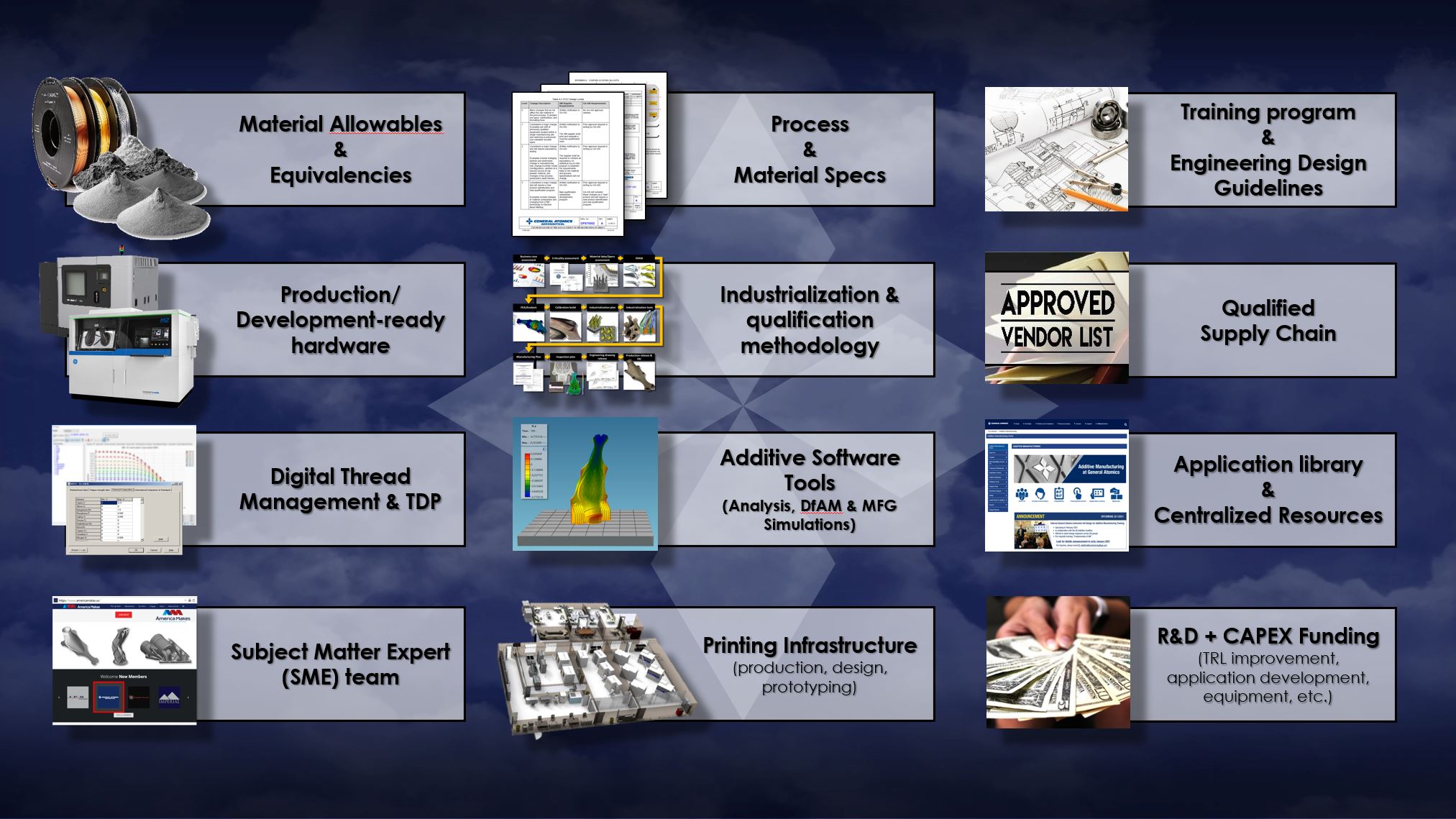
Après avoir mis en place une équipe et une stratégie de FA solides, GA-ASI a ensuite ouvert le centre d’excellence de conception et de fabrication additive (AD&M CoE) de la société en 2021. Le centre se concentre sur la fabrication à réaction rapide au service de la gamme de systèmes d’aéronefs sans pilote (UAS) de GA-ASI en utilisant des applications de fabrication additive (FA) entièrement fonctionnelles et prêtes à voler. En outre, ils soutiennent la recherche et le développement à des fins de réduction des risques appliqués liés à l’outillage à grande échelle, au matériel de vol existant et de prochaine génération.
Même si GA-ASI mène un large éventail d’activités de production récurrentes dans son centre d’excellence AD&M, Fournier souligne le fait que la demande de fabrication interne à réaction rapide et à faible cadence pour les programmes de développement du cycle de vie en phase initiale a obligé l’entreprise à s’appuyer sur une solide chaîne d’approvisionnement de fabrication additive pour la production excédentaire de pièces complexes en thermoplastique et en métal.
En parlant des objectifs que ces infrastructures servent à travers leur centre d’excellence de 790 m², Fournier explique :
« Nous tirons parti des capacités de fabrication rapide pour répondre à des demandes de faible à moyen volume sur des pièces métalliques, composites et thermoplastiques entièrement fonctionnelles (forme, ajustement et fonction). Il existe une distinction entre le prototypage et la fabrication rapide dans la profondeur des efforts de qualification requis pour les deux différents types d’utilisation de FA. Dans ce dernier cas, il faut qualifier les matériaux, la technologie et réduire tous les risques liés à l’application par une justification technique.
Le deuxième domaine d’intérêt est la R&D. Nous investissons dans les matériaux et les processus afin de qualifier les applications pour chaque technologie de FA d’intérêt. Par exemple, au cours des dernières années, nous avons investi d’importantes ressources dans la R&D pour qualifier les applications d’outillage utilisant la technologie de fabrication additive à grande échelle (LSAM), qui fait désormais partie de notre portefeuille de production. La R&D est réellement axée sur les applications et nous surveillons de près le retour sur investissement (ROI) à court et moyen terme.
Le troisième aspect de notre travail concerne la production récurrente. Nous fabriquons des pièces en plastique et en métal qui vont directement sur les avions après un processus d’assurance qualité approfondi. Nous conservons entre 15 et 30 % de notre demande de production en interne afin de maintenir nos processus et nos compétences au niveau de la production, et nous faisons appel à nos fabricants sous contrat qualifiés pour nos besoins de production excédentaire. Et cette production externalisée ne cesse d’augmenter. Notre principal objectif est de parvenir à une fabrication à réaction rapide en utilisant plusieurs technologies de FA, de faire passer les applications d’un niveau « ponctuel » à un niveau récurrent, et de fortifier notre chaîne d’approvisionnement pour soutenir notre croissance dans le domaine. »
Un portefeuille d’applications rendues possibles par la FA
Même si notre intérêt pour l’adoption de la FA par GA-ASI a été suscité par un cas d’utilisation réalisé avec la technologie LSAM de Thermwood, notre conversation avec le représentant de l’entreprise révèle comment ils ont développé plusieurs familles d’applications avec les technologies de FA.
Ces familles d’applications comprennent par exemple : des structures conformes, des conduits et des collecteurs de gestion de l’air, des couvercles et des panneaux, des composants de moteur et d’échappement, des montages de laminoir, des structures ultralégères, des outils de laminage, des composants OML et des échangeurs de chaleur. Ce ne sont là que quelques exemples que nous avons retenus de notre conversation avec Fournier. De nombreux autres sont actuellement à l’étude.
Quelle que soit l’application, l’équipe de GA-ASI a toujours gardé à l’esprit trois choses :
- Il est primordial de s’assurer de la validité de l’analyse de rentabilité avant de se lancer dans la technique (« imprimer parce que nous devons le faire, pas parce que nous le pouvons ») ;
- Les objectifs de fabrication prévus (s’agit-il de prototypage ou de production ? Il est essentiel de faire la distinction entre ces deux objectifs, car ils nécessiteront des efforts de qualification différents) ;
- et les exigences techniques qui déterminent le choix de la bonne combinaison de matériaux, de processus et d’approche de la conception.
Le cas de la production d’accessoires de laminoir réalisée en collaboration avec Thermwood
Si vous êtes un lecteur régulier de 3D ADEPT Media, vous savez probablement que Thermwood est l’une des rares entreprises à fournir du matériel et des services d’impression 3D très grand format avec des matériaux composites hachés en granulés de polymère renforcé de fibres (FPR). Avec un portefeuille croissant de machines, la société s’associe à un large éventail de producteurs de matériaux, d’industriels dans des secteurs verticaux adoptant la FA et d’universitaires pour explorer les applications qui pourraient déboucher sur des cas commerciaux viables pour sa technologie de fabrication additive à grande échelle (LSAM).
À propos de l’outil/support de découpe CNC, Scott Vaal, chef de produit LSAM chez Thermwood, explique qu’il « est généralement utilisé pour maintenir une pièce en plastique ou en composite de fibre de carbone formée en 3 dimensions pour des opérations de découpe secondaires telles que la forme finale du périmètre, les trous et les découpes. Les pièces sont généralement maintenues sur le dispositif à l’aide du vide ou d’une combinaison de vide et d’autres moyens de maintien mécaniques. « Plusieurs méthodes traditionnelles [sont souvent] utilisées pour fabriquer des outils/fixations d’ébarbage CNC, comme le collage de blocs de divers matériaux et leur usinage, le coulage d’un matériau de type coulé sur la face arrière d’une des pièces non ébarbées, et les structures de support en métal ou même en bois utilisées seules ou en conjonction avec la méthode des blocs coulés ou collés », ajoute-t-il.
Selon Fournier, le développement d’un outil de fixation de laminoir utilisant des procédés de FA vient du fait qu’ils voulaient explorer la faisabilité technique de la fabrication d’un tel outil moins cher et plus rapide :
« Nous avons commencé en 2017/2018 par sélectionner quelques projets de R&D liés à ce type d’outil (montages de laminage à température ambiante). Le principal défi à l’époque était de trouver un outilleur qui disposait de la technologie nécessaire pour explorer cette application. Même si nous avons commencé par travailler directement avec l’équipe d’application de Thermwood, nous avons commencé peu après à travailler et à qualifier les outilleurs qui utilisent la technologie de Thermwood. »
Compte tenu du prix de l’imprimante 3D, il était risqué pour GA-ASI de commencer par investir dans une technologie sans avoir la certitude qu’elle permettrait de réaliser les analyses de rentabilité qu’elle souhaitait mettre en place. Sans compter qu’une fois l’imprimante 3D obtenue, il faut disposer d’une main-d’œuvre qualifiée capable de faire fonctionner la machine, de tout l’équipement de pré- et post-traitement qui pourrait aider à livrer la pièce désirée, ainsi que des installations adéquates pour accueillir ce type d’équipement de grande taille.
« Compte tenu de tout cela, la plupart des entreprises ont besoin de beaucoup de capitaux pour se lancer dans cette technologie. C’est pourquoi notre stratégie n’a pas consisté à acheter une imprimante tout de suite, mais plutôt à développer nos partenaires de la chaîne d’approvisionnement. Le développement et la qualification de l’application nous ont aidés à créer le « signal de demande » pour les applications qui pourraient être satisfaites en internalisant potentiellement cette technologie à un coût d’infrastructure et de ressources important. Après nous être convaincus que les exigences techniques pouvaient être satisfaites pour les applications d’outillage de fixation d’usine, nous avons depuis étendu notre utilisation de la technologie LSAM au-delà des cas d’utilisation d’outillage, et nous poursuivons notre investissement dans notre chaîne d’approvisionnement », explique Fournier.
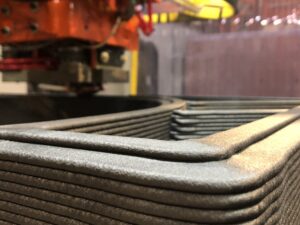
La période d’exploration de ce dossier commercial a duré environ 2 à 3 ans. Elle a été marquée par de nombreux tests et essais de fabrication avant de conclure qu’il s’agissait d’un outil viable pour la production. Le processus d’impression 3D du dispositif de fixation de la fraise a pris environ 16 heures et a nécessité l’utilisation d’une Thermwood LSAM 1200 qui a traité un matériau ABS (chargé de 20 % de fibre de carbone). Le processus de post-usinage des surfaces critiques de l’outil a pris beaucoup plus de temps. Dans l’ensemble, le processus a permis d’obtenir un outil final pesant 540 kg (1190 lbs).
« Le procédé LSAM est disponible en plusieurs modèles, tailles et configurations pour répondre à une variété de besoins. Chaque LSAM est équipé du même système unique et breveté Melt Core qui peut traiter et imprimer une grande variété de matériaux pouvant être utilisés pour des applications à température ambiante jusqu’à des matériaux à haute température pouvant être utilisés pour l’outillage d’autoclave aérospatial qui doit dépasser 350 degrés Fahrenheit [177 °C]. À ce jour, nous ne connaissons pas de matériau pratique que le LSAM ne puisse traiter et imprimer », rappelle Vaal avant de commenter la production : « Cette pièce était assez simple du point de vue de l’impression et s’est très bien prêtée au processus. Le seul véritable défi se situait du côté de la toupie CNC à 5 axes. Le dégagement de la tête de la fraiseuse n’était pas suffisant pour usiner des rainures d’étanchéité sur une bride d’environ 2 pouces de large à une extrémité de la pièce. Nous avons donc fini par diviser et imprimer la section de la bride séparément pour pouvoir usiner facilement la bride et les rainures, puis la coller à la section principale avec précision en utilisant des trous de positionnement de goujons pour terminer la pièce. »
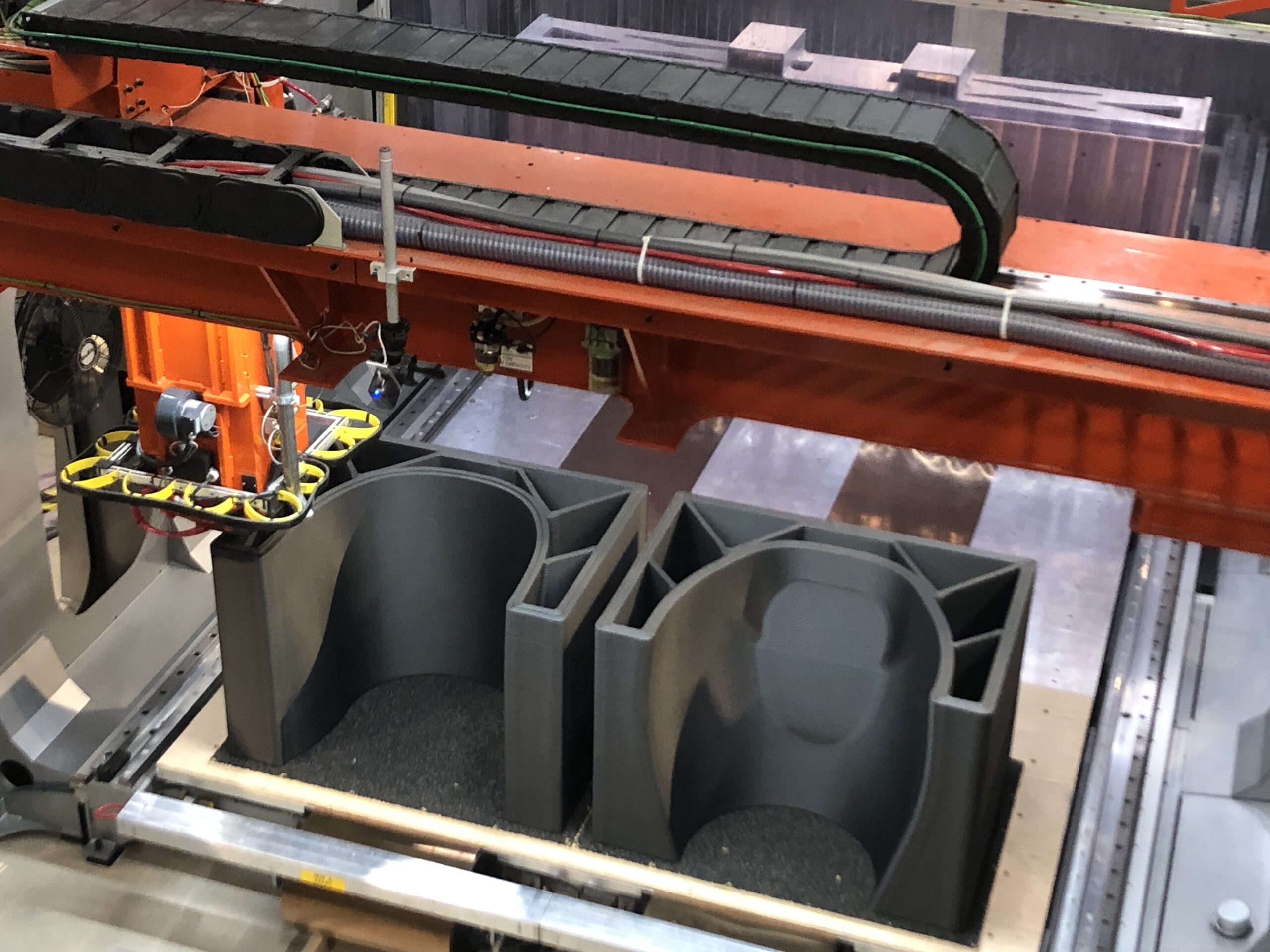
Il est intéressant de noter que cette application aurait permis à GA-ASI de réaliser des économies d’environ 50 000 $ (46 192 €) par rapport aux méthodes traditionnelles.
Le calcul de ces économies peut être assez simple de nos jours : « Pour les applications d’outillage, par exemple, il est possible d’obtenir des devis de plusieurs fournisseurs pour les options conventionnelles et additives, et de faire la comparaison à partir de là. Cependant, l’aspect conception du travail peut parfois faire une différence significative dans le processus d’établissement du devis. Au fil du temps, vous accumulez suffisamment de statistiques sur les géométries de plusieurs outils pour commencer à obtenir une mesure du coût par surface de la feuille de surface de l’outil. Il s’agit d’une mesure typique utilisée dans l’industrie de l’outillage. Il est important de noter que ces analyses de rentabilité peuvent être très différentes selon la géométrie des outils. Tous les outils ne sont pas les mieux adaptés à la technologie LSAM. Les fabricants de machines, quant à eux, ont une méthode de calcul différente, car ils doivent tenir compte de l’amortissement de la machine, du personnel nécessaire, des matériaux, etc. mais ils se résument essentiellement à un dollar par livre ou par pied carré », souligne Fournier.
Avance rapide jusqu’à aujourd’hui : le LSAM de Thermwood permet d’aller au-delà des montages en usine.
Aujourd’hui, GA-ASI a développé une équipe interfonctionnelle d’experts en la matière au sein de plusieurs fonctions d’ingénierie, de qualité, d’approvisionnement et de fabrication, et continue d’investir dans cette technologie afin de réduire les défis techniques et commerciaux supplémentaires rencontrés au fur et à mesure qu’elle élargit l’espace d’application de cette technologie.
« Aujourd’hui, nous faisons à la fois de l’outillage pour de grands montages d’usine à température ambiante, en explorant des applications à plus haute température, et aussi des pièces d’utilisation finale pour de très grandes structures. Chaque application comporte son lot de défis », souligne Fournier.
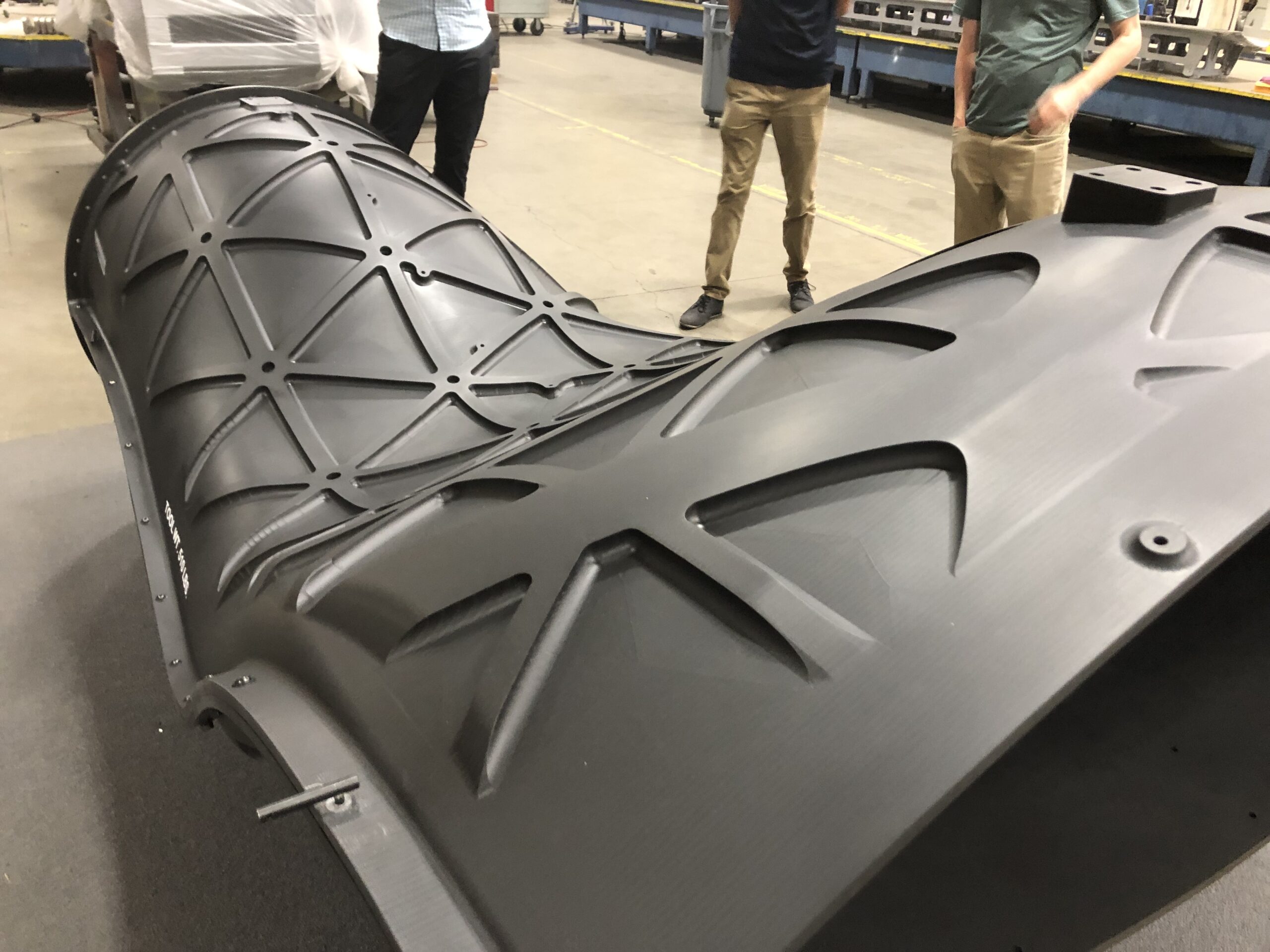
« Nous poussons également notre recherche du côté des températures plus élevées, avec un outil de laminage. Pour de telles applications, l’un des défis importants et limitatifs de cette technologie est le CTE », note-t-il. [Le coefficient de dilatation thermique (CTE) décrit comment la taille d’un objet change en fonction de la température. En d’autres termes, cette propriété matérielle indique dans quelle mesure un matériau se dilate lorsqu’il est chauffé]. En termes simples, et sans trop creuser dans les détails techniques, la nature anisotrope des propriétés du matériau imprimé crée des problèmes d’application de lamination. Par exemple, l’expansion thermique le long de l’axe XY est très différente de celle mesurée le long de l’axe Z. Cela entraîne des problèmes de stratification potentiellement importants. Cela entraîne des problèmes de laminage potentiellement importants sur l’intégrité de l’outil et de la pièce, en fonction des plages de température et des géométries de la face de l’outil.
« En raison des propriétés anisotropes, pour certaines géométries d’outils de laminage, la technologie LSAM pose des défis importants dans la conception de l’outil pour pré-compenser et contrôler la forme de l’outil pendant le cycle thermique, ainsi que pour le processus de démoulage qui peut avoir un impact sur l’intégrité de la pièce laminée elle-même. Au final, les risques techniques DOIVENT être mis en balance avec les avantages apportés par la technologie de fabrication utilisée. Cette technologie particulière est bonne et bénéfique pour les applications à température ambiante. Même à température ambiante, l’espace d’application est limité à une certaine catégorie de géométries d’outils et de structures d’utilisation finale. Avec l’aide de nos partenaires de la chaîne d’approvisionnement, nous repoussons maintenant les limites de l’espace d’application pour voir ce qui peut être bénéfique – d’un point de vue commercial », complète-t-il.
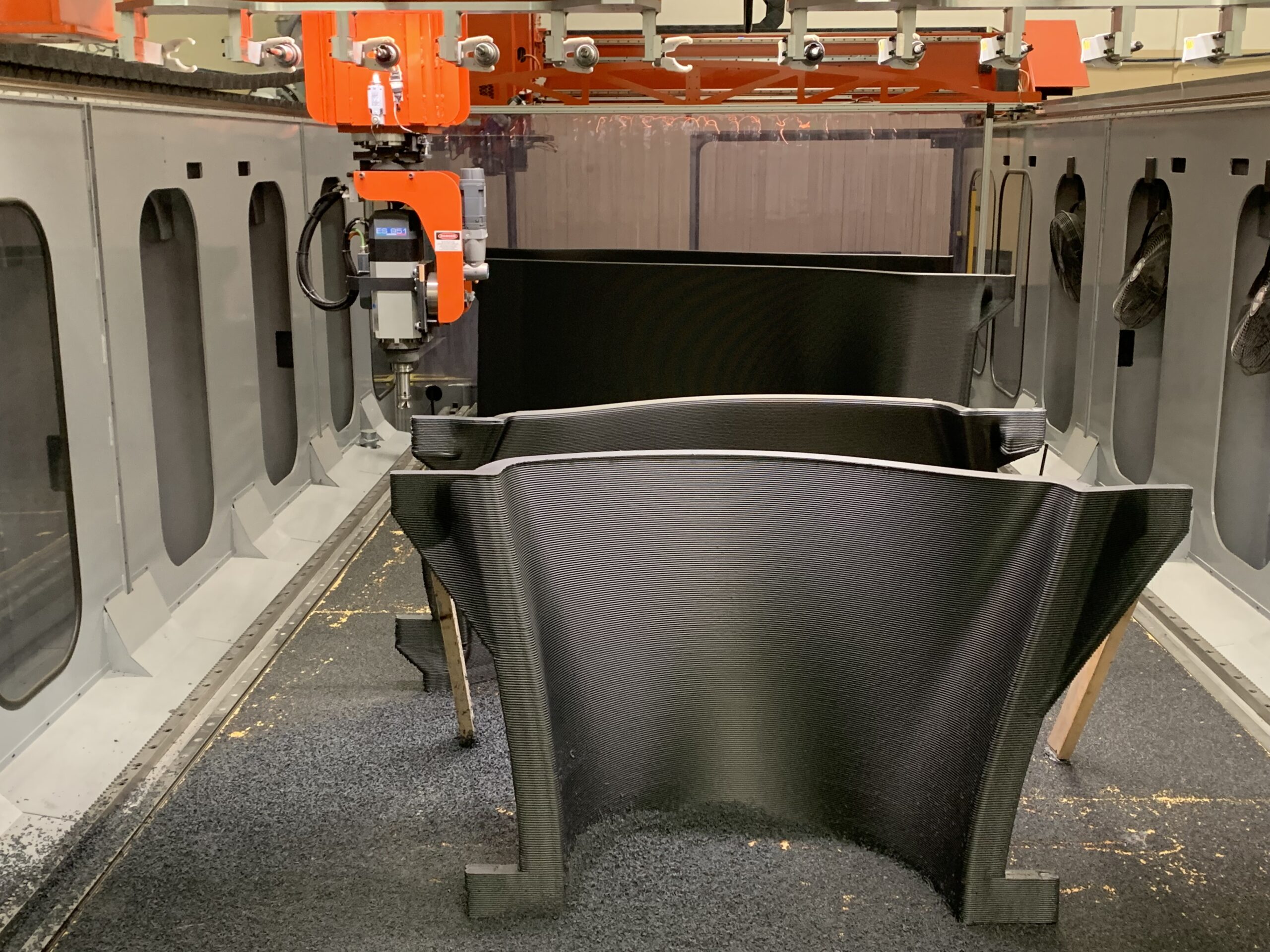
L’aventure continue
La mise en œuvre des technologies de FA dans l’industrie de l’aviation et de la défense est un long voyage qui se poursuit « une application à la fois ». Au cours de ses 15 années d’expérience avec la FA, Fournier a partagé quelques-uns de ses apprentissages :
- Chaque industrie, et chaque utilisateur au sein d’une industrie donnée, a des ensembles d’applications spécifiques, et il est important/critique d’identifier les avantages commerciaux au niveau global pour aider à motiver l’investissement de capital et de ressources pour amener la FA au niveau où ces avantages peuvent être réalisés.
- De nombreuses technologies de FA ont atteint un niveau industriel et peuvent être utilisées pour des applications prêtes à la production avec des contrôles appropriés et suffisants. D’autres nécessitent la poursuite de la mise en place d’éléments de l’écosystème de la FA, tels que des normes et une meilleure ingénierie des équipements. Mais la FA ne doit pas être l’objectif final. La FA est un outil puissant qui fait partie d’une vaste boîte à outils qu’elle combine également avec des technologies conventionnelles. La clé du succès consiste à trouver les bonnes applications pour la FA.
- Il a été bénéfique pour GA-ASI d’investir dans la constitution d’une équipe d’experts en la matière avant d’investir dans l’infrastructure et l’équipement, afin de construire une feuille de route solide pour l’écosystème de la FA et d’établir ses propositions de valeur.
- Les cas d’utilisation de la FA peuvent être résumés, par ordre croissant de proposition de valeur, comme suit : a) substitution de pièces pour obtenir des avantages au niveau des composants ; b) consolidation de pièces pour éviter les assemblages et les coûts associés, ce qui conduit à c) des solutions de conception pour la FA (DfAM) nouvelles et uniques, qui peuvent atteindre le niveau du sous-système. De même, il ne faut pas sous-estimer les solutions de soutien dans la dernière phase du cycle de vie de nos produits.
« En général, je décris la FA comme une technologie analogue à celle des « voitures de luxe »… Lorsque nous envisageons de nouvelles applications pour la FA, nous nous demandons toujours : pourquoi la FA ? L’utilisation d’une technologie de niveau « voiture de luxe » nécessite de trouver une application et des avantages équivalents de haut niveau. Cela signifie pour nous, chez GA-ASI, plus d’intégration de pièces, des conceptions encore plus performantes et une réduction des coûts de fabrication. Pour y parvenir, il faut généralement créer de nouvelles conceptions plus complexes dont le coût et les exigences en matière d’outillage augmentent avec les procédés de fabrication conventionnels, alors que l’AM est en mesure de gérer ces conceptions complexes avec une différence de coût minime, voire nulle, et souvent sans avoir besoin d’outillage. Il s’agit d’utiliser la FA pour les bonnes raisons », conclut Fournier.
GA-ASI a déjà été en mesure d’économiser des millions de dollars en outillage non récurrent et d’économiser des coûts récurrents très importants sur ses plateformes d’aéronefs. En continuant à repousser les limites de l’applicabilité des diverses technologies de la FA et en explorant de nouvelles applications, GA-ASI prévoit de pouvoir intégrer davantage de pièces et, à terme, d’augmenter le pourcentage de contenu de la FA sur ses plates-formes d’aéronefs de <1% à 75% selon la classe de l’aéronef et son niveau de survie, d’éviter l’outillage lorsque cela est possible dans le processus de fabrication de ses composants, et de contribuer à apporter de nouvelles solutions d’outillage de la FA lorsque cela est nécessaire.
Cet article a été initialement publié dans le numéro de Janvier-Février de 3D ADEPT Mag.