Medicrea is a company that specializes in the design and production of medical devices for spine cord surgery (the spine). To manufacture their products, they use both conventional methods, such as machining, and new processes, such as printing.
They integrated 3D printing technology at the end of 2014. Over time, they have developed the “design” part in the design of their products and since the integration of 3D printing, they have also strongly developed R&D in the production of implants.
From the beginning of the integration of 3D printing, the idea was to make the production customisable … However, there are two main activities that they carry out today using 3D printing: the production of customized and standard implants.
Medicrea took part in the dossier of the April issue of 3D Adept Mag, our magazine, dedicated to the 3D printing industry. Discover, the whole interview in this Opinion of the Week.
What drove the adoption of this technology to produce implants?
Medicrea is very focused on innovation and R&D. It’s in our DNA to produce differently and find ways to produce implants with more complex shapes, and geometries that integrate quickly into the body.
Our implants allow to quickly create the fusion between the vertebrae. The idea is to have easy surface properties to resistance by bone while properly integrating the mechanical properties.
Moreover, 3D printing allows us to have the freedom of design for forms that are not always adapted.
And for mass production, we have the ability to produce implants that are more suited to specific needs compared to those made with machining. So, we have some flexibility in the production: for a small quantity, we can detail 100 pieces in several lots for example …
We use the manufacture of metal powder (titanium), SLM machines that allow the use of the laser melting technique and therefore the possibility of making solid implants.
Can you share with us some feedback on the opinion of doctors on the use of a 3D printed implant in a patient? What about the patient’s opinion?
For customized implants, the technology makes it possible to make very suitable implants. These are the most complex implants, having something customized facilitates “the operative gesture”. Implants adapt better to structures because they provide a solution that does not exist and produce an ideal post-operative result.
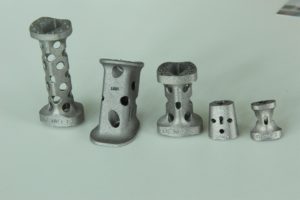
At the level of more standard ranges, it must first be understood that the product offering is based on customization and planning.
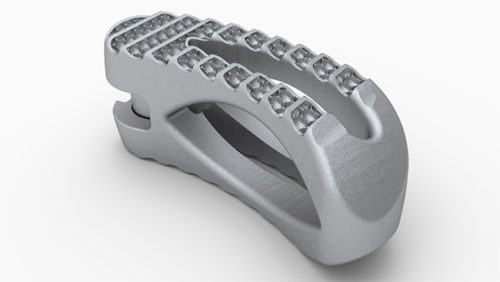
We have doctors working on algorithms for customization.
For planning, however, surgeons can choose implants … The surgeon has the choice to adapt it to his needs, the pathology he wants to treat, which is possible with 3D printing as it is flexible. Standard and personalized implant.
As far as patients are concerned, there has never been a case which has resulted in failure.
What are the advantages and limitations of this technology?
Advantages: at the series production level – freedom of form, possibility of doing more technical things, possibility of making small series of parts.
For projects under development – possibility to make prototypes. We have more agility in the way we work and we move quickly in the design phases.
Limitations: As we use technologies that require the use of titanium, the limits we face concern the control of the material. For a company that enters the market in 2014, this may slow down some projects because the integration of 3D printing requires the acquisition of new skills, the establishment of security means for the sensitive material that must to be used under certain conditions.
What are the prospects of development for Medicrea?
Knowing that today, we have a range that was put on the market last year after almost two years of R&D. Here, our goal is to take advantage of this experience, to make new implants that have other features.
We must push the limits to achieve the best performance. We must therefore gain maturity.
For further information, follow us on our social media and subscribe to our newsletter!
Would you like to be featured in the next issue of our digital magazine? Send us an email at contact@3dadept.com