A team of Penn State researchers discovers how 3D printing can improve cell adhesion and strength of PDMS polymer. The mix of two different polymer forms can switch manufacturing of silicone parts from molding, casting and spin coating of simple forms to 3D printing of complex geometries. These geometries integrate better mechanical characteristics and biological adhesion.
The problem is that PDMS (polydimethylsiloxane, or silicone) presents limitations in formability and manufacturing of devices.
How they take advantage of the material?
PDMS is used to make lab-on-a-chip devices, organ-on-a-chip devices, 2 and 3D cell culture platforms, and biological machines. The material is more commonly seen as heat-resistant silicone spatulas and flexible baking pans, but these are geometrically simple and can easily be molded. If the material is used for growing tissue cultures or testing, the geometries become much smaller and more complex.
Using a 3D printer, the material must be able to go through the printing nozzle and maintain shape once it is deposited. The material cannot spread, seep or flatten or the integrity of the design is lost. Sylgard 184, an elastomer of PDMS, is not viscose enough to use in 3-D printing — the material simply flows out of the nozzle and puddles. However, when it is mixed with SE 1700, another PDMS elastomer, in the proper ratio, the mixture is printable.
To carry out the research, the team obtained patterns for biological features — hands, noses, blood vessels, ears, and femoral head, from the National Institutes of Health 3D Print Exchange.
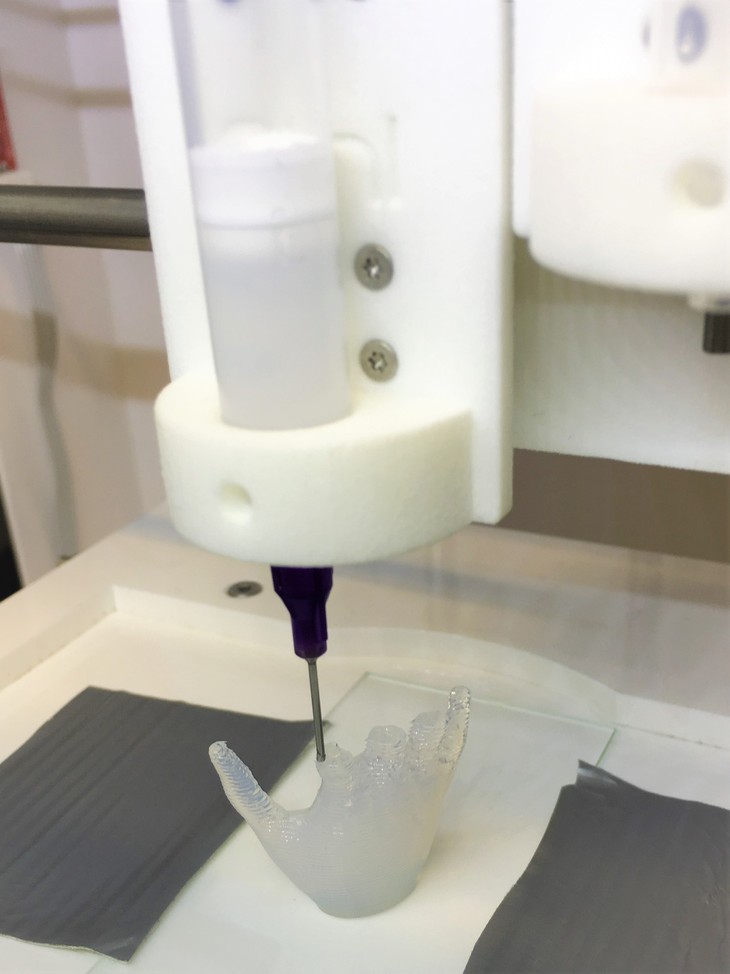
They 3D printed a nose as part of their study. Notice is to be made that such an organ can be printed without support materials and include hollow cavities and complex geometries.
“We coated the PDMS nose with water and imaged it in an MRI machine,” said Ozbolat, a contributor to the research. “We compared the 3-D reconstructed nose image to the original pattern and found that we had pretty decent shape fidelity.”
“When we compared the mechanical signatures of molded or cast PDMS with 3-D printed PDMS, we found the tensile strength in the printed material was much better,” added Ozbolat.
For further information about 3D Printing, follow us on our social networks and subscribe to our newsletter!
//pagead2.googlesyndication.com/pagead/js/adsbygoogle.js
(adsbygoogle = window.adsbygoogle || []).push({});