Over the past 40 years since the introduction of 3D Printing, 3D Printer manufacturers have been looking for various solutions to improve technology and achieve the right first-time additive manufacturing process. They have been addressing issues at various levels: software, hardware, materials but they rarely considered the production environment.
As we write these lines, we cannot help but think about what we learned during this trip we took to Sweden to visit an additive manufacturing (AM) plant: part of building a great company is having the right facilities and the right tools for the teams, customers and suppliers to work with, and developing the best possible products. In industries that require a production environment, this means understanding how external elements can impact the manufacturing process and the working environment and learning how to “manage what seems to be out of control”: dusts, fumes, odours, gases and vapours.
The issue might seem trivial yet is crucial and addressing it the right way can literally help any manufacturer save money. Companies that are uniquely positioned to understand such a situation are air technologies providers, and an exchange with ULT AG tells us how.
“THREE DECADES LATER, AN ENTREPRENEURIAL MINDSET AND A MULTIFACETED PORTFOLIO”
Put simply, ULT AG, short for Umwelt-Lufttechnik (environmental air technologies), specializes in extraction, filtration, and air-drying technology. The company’s journey started 26 years ago in Löbau (Germany) with the single goal of removing hazardous particles in various manufacturing processes including laser processes, soldering operations or welding processes, to name a few.
More than two decades later, a well-established international customer base and distribution network, and a 130 certified staff in DIN EN ISO 9001, we rediscover a company whose entrepreneurial mindset has led to the development of a multifaceted portfolio.
“The company’s solution portfolio ranges from mobile extraction units for manual workstations and tasks under limited space, stationary systems that can also be integrated into production lines, to complete hall extraction or support of large systems.
In addition to turnkey solutions, ULT AG develops and produces special devices for particular applications. That happens in close cooperation with the customers. ULT does not sell systems but provides solutions that fit best with the respective application. If required ULT develops customer-specific fume extraction systems, also certified according to ATEX and W3 and tested to meet H requirements.
In support of capturing efficiency, ULT provides extraction elements and suction arms, designed for specific working situations and applications”, states Alexander Jakschik, Managing Director/CTO at ULT AG.
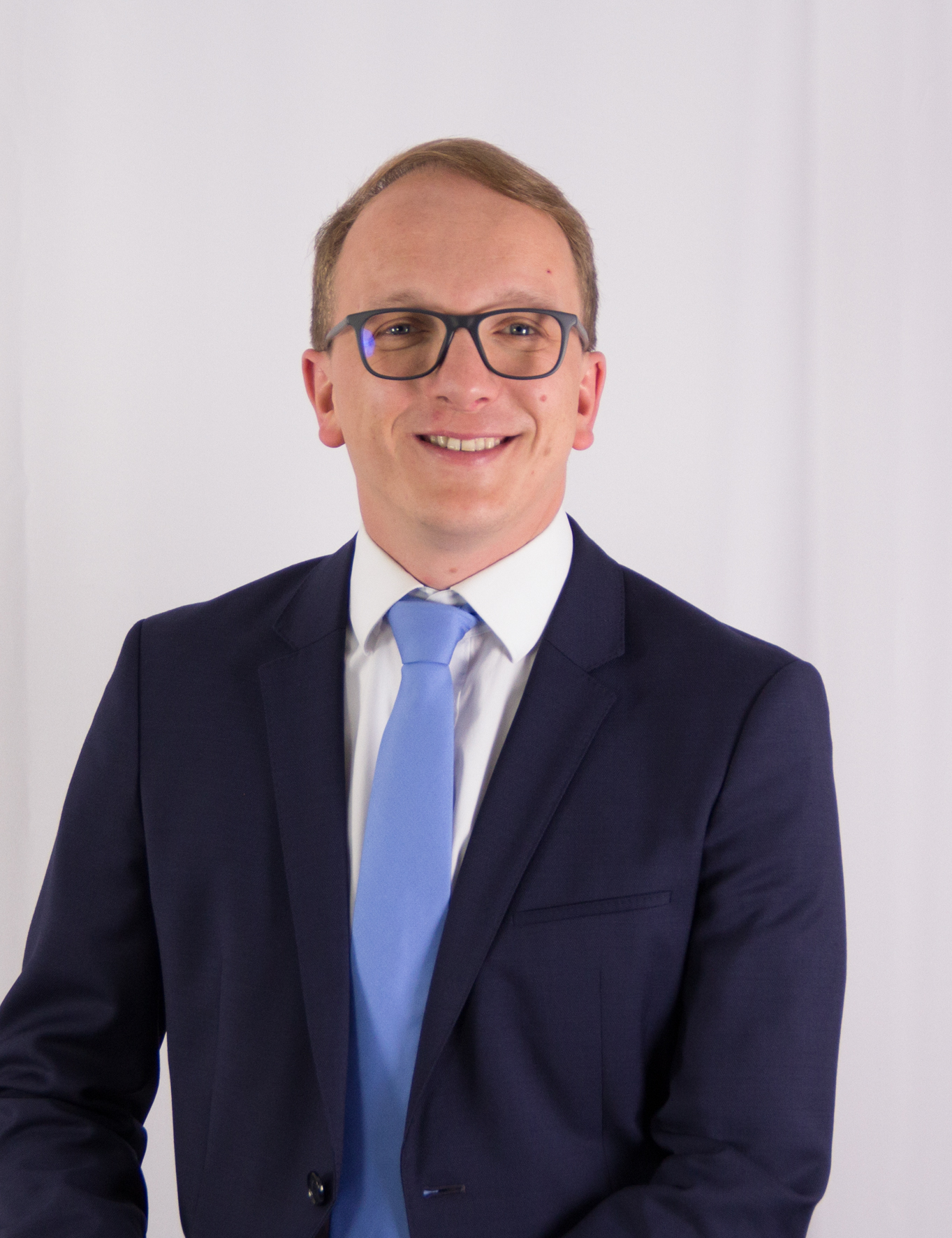
Over time, research shows that every plant is unique and needs to meet many specific requirements for optimal comfort to be obtained. Manufacturing facilities for instance, are high-bay buildings, which sometimes require both heating and ventilation systems. Such constraints mark the beginning of ULT’s collaborative efforts with engineering offices to develop complete air handling systems.
More importantly, as there is always room for improvement, the air technologies specialist has made cooperation with research institutes and universities a top priority. At present, the company has created a global network for research and development issues, especially in the fields of future technologies and processes.
Very early, the first tangible AM applications unconsciously marked the importance of gas cleaning to process argon and nitrogen, inert gases which are usually present in the production environment. Interestingly, as the market is still considered a nascent one, it is crucial to develop a dedicated product offering whose focus would be advice and product assessment on everything related to air pollution control, occupational safety, air drying in plastic and metal AM processes.
“ADVICE & PRODUCT ASSESSMENT”
“ULT has always been a company that was very early on adapting to technological changes and innovations. We have always been one step ahead in technology. It was the same 20 years ago when the first AM applications appeared, and we needed gas cleaning to process argon and nitrogen. Since then, we have consistently developed our product portfolio in this area”, explains Boris Fruehauf, Key Account AMF with ULT.
In this vein, the additive manufacturing industry can benefit from inter gas cleaning in laser sintering, laser melting, laser applications as well as in similar processes. It can also take advantage of process air drying for powder handling which ensures good process quality of the powder. Furthermore, ULT can advise and provide fume extraction solutions for powder handling, at post-processing workplaces, as well as industrial vacuum cleaner for cleaning construction chambers and the entire ventilation technology concepts for sites using additive manufacturing.
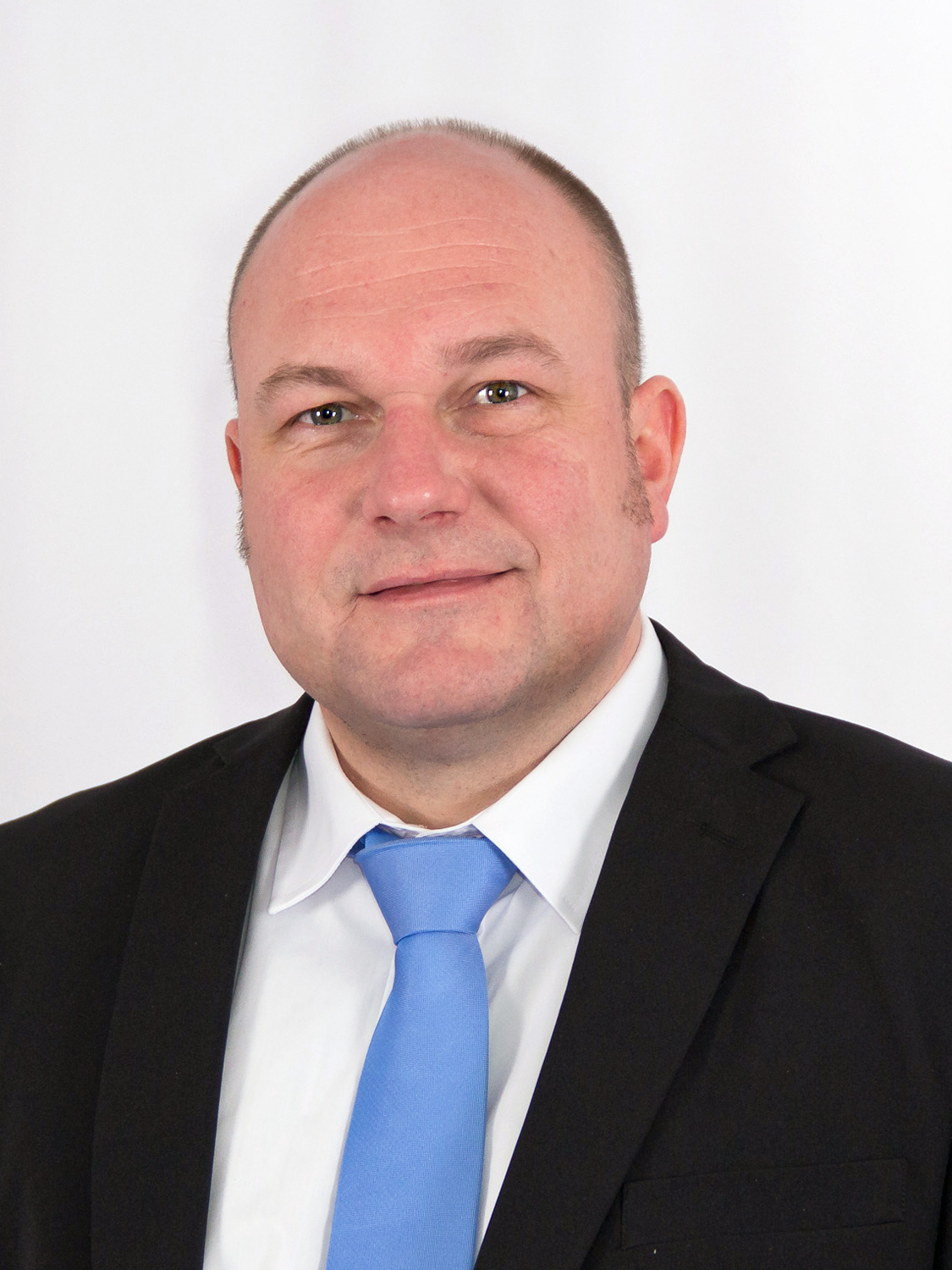
THE DEVIL IS IN THE DETAIL
ULTs aforementioned commitment to the additive manufacturing industry is clearly stated: advise, assess and customize when possible. In theory, ULT AG has understood the needs of the market and has developed a wide range of services that this market can take advantage of, but in practice, the market is very far from having understood where the issue is.
It’s already been three years that we ask additive manufacturing experts what they expect for every new year, and the common thread of all responses is to be able to move AM to series or mass production. We are almost there but not yet. Laudable improvements have been made at every level (material, hardware and software) but not at this one. In the end, reality shows that it’s a matter of awareness. Air treatment is to production environment what materials are to 3D Printers.
“It does not work without it. Gas cleaning is essential for a functioning process. The difficulties lie in the details and, hence, it shows that many companies with 3D printers after the initial «gimmicks» and gaining experience are now reaching their limits with large construction jobs or series production. Some still have this learning curve in front of them and try to improve it. ULT can help and provide solutions based on many years of know-how in industrial extraction and filtration technologies.
But one thing should be said, there are no standard systems that fit all types of 3D printers in the PBF or SLM process, these are always special adaptations. However, the ULT has advantages in this area because it uses standard components from modular systems. These are constantly being further developed and this also includes extraction accessories, e.g. for post-processing, or on topics such as air drying that play a major role in preventing corrosion of steel powders. The world of extraction in the AM plastics area is still at the very beginning. The industry has just started to take air cleaning or the filtration of harmful substances and smells more seriously” continues Fruehauf.
Luckily, this is just the beginning. Metal additive manufacturing users and machine manufacturers of powder-bed fusion technologies and Selective Laser Meting technologies are leading the learning curve but there is still a long road to go as plastic SLS, FDM and SLA 3D printers’ users increasingly face issues related to gas cleaning.
Harnessing gas cleaning solutions is a big move, but one which will enable any large manufacturer to bring safety, quality, turnaround time and costs into its direct focus. The issue took a certain amount of time before it comes through the pipeline, but it has now and ULT AG is looking forward to contributing on this field with its air technologies solutions.
This content has been written in collaboration with ULT AG.