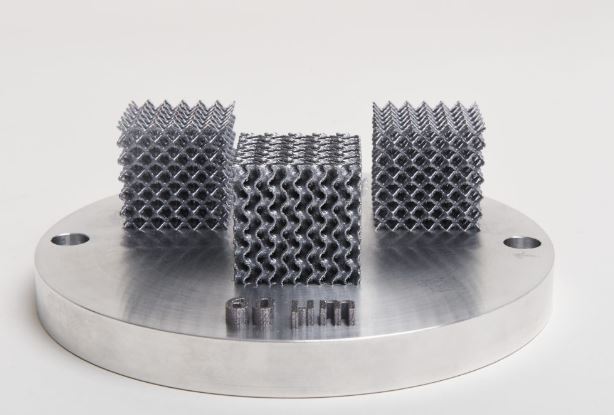
Material producer Equispheres Inc. and 3D printer manufacturer Aconity3D pushed the limits of their 3D printing machines and materials, building on their previous announcement of improving the metal 3D printing production speed by 3x. They used Aconity3D printing equipment with laser beam shaping and Equispheres’ NExP-1 AM powder to achieve an enhanced production speed, exceeding the 430 cm3/hr for a single laser.
They claim they can achieve build rates about 9x greater than industry norms for aluminum powder and laser powder bed fusion.
Speaking about that, Vice President of Product & Strategy at Equispheres Evan Butler-Jones said: “There are three pillars supporting this remarkable achievement. The leading-edge capabilities of Aconity3D’s printing technology, the novel application of beam shaping, and the unique powder properties of Equispheres’ NExP-1 printing material. This powerful combination allowed us to achieve outstanding results.”
Improving LPBF speed with laser beam shaping
The laser beam shaping technology is already popular in different industries and now the AM industry is warming up to it to improve processing speeds. This technology in the laser powder bed fusion modifies how energy is deposited on the powder bed, ultimately altering the thermal gradient and power density.
Equispheres and Aconity3D used a 3D printing material with stable melting behavior to leverage the full potential of laser beam shaping along with the use of a controlled printing process.

While the NExP-1 is a AlSi10Mg powder by Equispheres offers consistent and repeatable melting properties, the AconityMIDI+ modified with an IPG YLR 3000/1000-AM with beam shaping capabilities enabled 3 kW of maximum power for this project.
The use of a shaped beam helped in reducing overheating and spatter formation which is a problem in zoomed gaussian beam usage during high productivity processing.
“Aconity3D’s printing technology and the team’s expertise were crucial to this project’s success. We’re working with extremely high-powered lasers, testing additive manufacturing process parameters far beyond previous capabilities. It was necessary to have the precise control and monitoring capabilities of Aconity3D printers,” said Butler-Jones.
Martin Buscher of Aconity3D said: “NExP-1 powder has properties that make it ideal for high-speed work. The powder characteristics enable optimal melting behaviour, which is required to achieve consistent printing with high-powered lasers at these extraordinary speeds”.
The two AM companies illustrated how high production speeds in aluminum L-PBF could be achieved by combining engineered beam profiles and powders at Formnext 2023.
Remember, you can post job opportunities in the AM Industry on 3D ADEPT Media free of charge or look for a job via our job board. Make sure to follow us on our social networks and subscribe to our weekly newsletter : Facebook, Twitter, LinkedIn & Instagram ! If you want to be featured in the next issue of our digital magazine or if you hear a story that needs to be heard, make sure to send it to contact@3dadept.com