Daimler, parent company of Mercedes-Benz and Setra 3D printed over 780 customized automobile parts for customers.
The leader in the bus and the coach sector prints complex parts located in the bus interior in a single step, which formerly consisted of several and in some cases even moving components.
Daimler has been active in 3D printing for 25 years. The group recently got a Ricoh Selective laser sintering machine.
The advantage of selective laser sintering is that it combines speed, flexibility, economy and ecology in its proposal. Daimler does not only meet the needs of customers, they also meet the spare parts requirements. This is in direct contrast to the injection molding technique which requires “costs related to the production of tools, the storage of components and the disposal of surplus materials.“
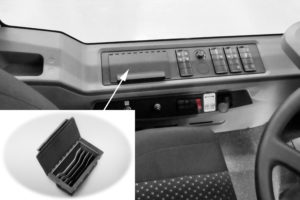
3D printed separated parts
The cash storage compartment, for instance, shows the advantages of reducing parts manufactured separately.
Geometry, on the other hand, allows an enormous flexibility. It is possible to easily change the volumes. This is precisely the case in small series involving lot sizes from 1 to 50 units.
Moreover, to bring the whole process to life, it is only a matter of a few days.
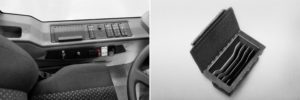
“In the medium term, we see digital production technologies as harbouring vast potential to enable us to address market and customer requirements in a flexible manner while at the same time minimising investment risks,” says Hartmut Schick, Head of Daimler Buses.
//pagead2.googlesyndication.com/pagead/js/adsbygoogle.js
(adsbygoogle = window.adsbygoogle || []).push({});