To provide more solutions to industrial companies, Bright Laser Technologies (BLT) has introduced a high-strength aluminum for Selective Laser Melting (SLM) and the BLT-Ti65 powder for Selective Laser Melting (SLM) and Directed Energy Deposition (DED) processes. Each of these materials integrates properties that could serve for a wide range of applications across industries using AM.
Key specifications of the BLT-AlAM500 high-strength aluminum
The challenge with high-strength aluminum is that they could lead to cracking and poor density during the manufacturing process. The metal 3D printer manufacturer has therefore optimized the process parameters for its BLT-AlAM500 high-strength aluminum – overcoming the challenges in the manufacture of large-size parts with integrated structures and achieving optimal yield rates.
The new material could serve for the fabrication of aerospace and aircraft structural parts as well as engine parts. Beyond aerospace, high-strength aluminum alloys are also essential in high-speed trains, lightweight automotive parts, and premium sports equipment.
To highlight the characteristics of the new material, the manufacturer shared the example of a bent tube, a ventilation duct and a connecting pipe it manufactured.
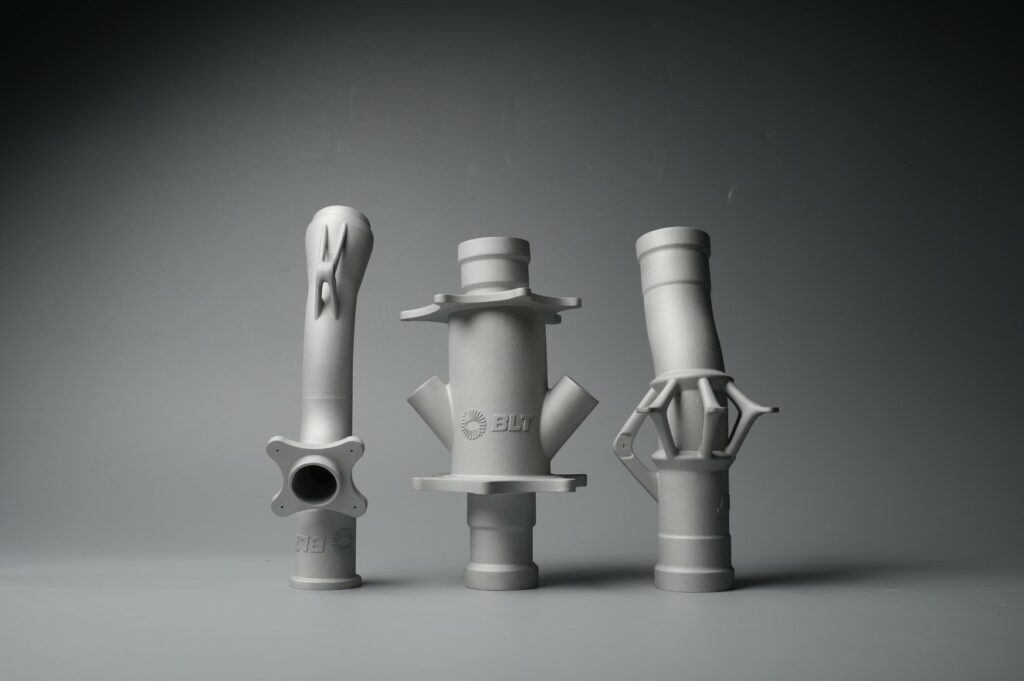
A press communication explains:
These components, characterized by thin-walled, irregularly shaped tubular structures with internal cavities, demand high precision and quality. BLT optimized the design of these parts, using the high-strength aluminum alloy BLT-AlAM500 and its Metal LPBF printing machine BLT-S400 for manufacturing. Each part takes approximately 30 hours to form, achieving an average weight reduction of around 20%.
Post-heat treatment, the material achieves tensile strengths of 530-550 MPa, yield strengths of 480-500 MPa, and elongation rates of 11-17%. The material also boasts excellent fracture toughness and fatigue performance, with a room temperature fracture toughness of 30.8 MPa·m1/2 and a high-cycle fatigue strength of 245 MPa (smooth sample) at room temperature. Compared to similar imported powders, the BLT-AlAM500 material offers a cost reduction of about 40-50%, significantly lowering manufacturing costs.
Key specifications of the BLT-Ti65 powder
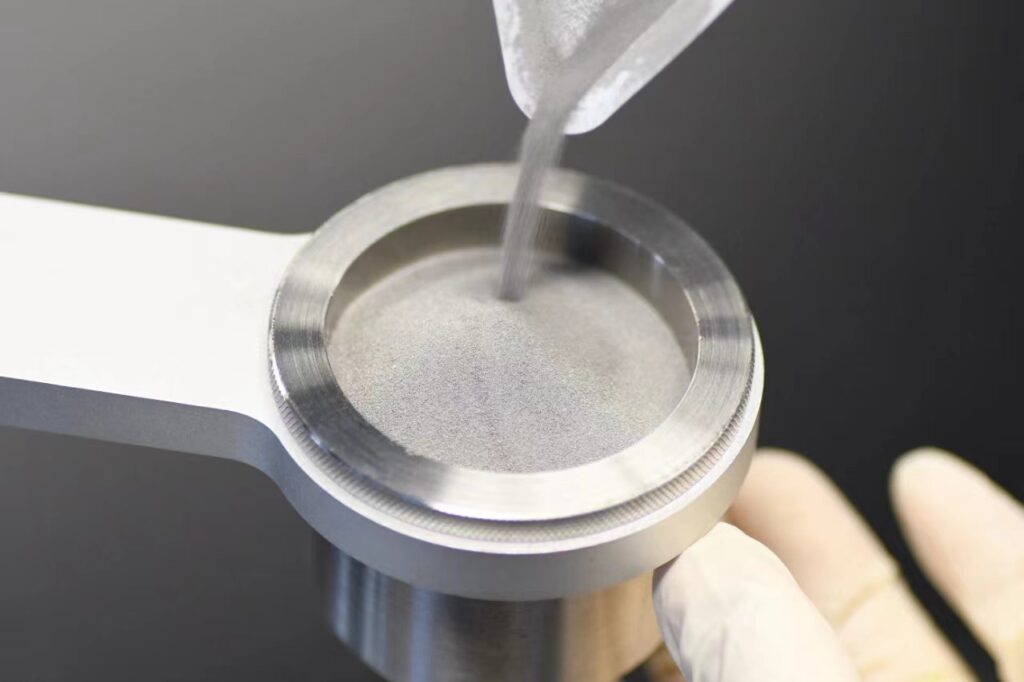
Designed for LPBF and DED processes, this multi-component near-alpha high-temperature titanium alloy would be ideal for aerospace, chemical equipment, and marine engineering applications.
During its development, BLT took into account the fact that the AM production of Ti65 may often lead to defects like unmelted or partially melted powder particles, inter-track and inter-layer porosity, and cracking, which can concentrate stress and increase the likelihood of material failure.
The nominal chemical composition of BLT-Ti65 is Ti-5.9Al-4Sn-3.5Zr-0.3Mo-0.4Si-0.3Nb-2.0Ta-1.0W-0.05C, available in 15-53μm (for SLM) and 75-180μm (for DED). Post-heat treatment, parts produced with 15-53μm BLT-Ti65 powder can achieve yield strengths of 483-503 MPa, tensile strengths of 604-624 MPa, and elongation rates of 16.5%-26.5% at 650°C. Parts produced with 75-180μm BLT-Ti65 powder can achieve yield strengths of 478-538 MPa, tensile strengths of 588-648 MPa, and elongation rates of 22%-32% at 650°C, the company says.
Remember, you can post job opportunities in the AM Industry on 3D ADEPT Media free of charge or look for a job via our job board. Make sure to follow us on our social networks and subscribe to our weekly newsletter : Facebook, Twitter, LinkedIn & Instagram! If you want to be featured in the next issue of our digital magazine or if you hear a story that needs to be heard, make sure to send it to contact@3dadept.com