Chinese technology company Atomstack unveils a new series of 3D printers that can process thermoplastic rubber (TPR) filament.
First 3D printers of this series are the Cambrian Pro and Max extrusion machines that have been designed with makers and professionals in mind.
Both machines share similar features such as printing speeds of up to 100mm/s and differ in build volume (235 x 235 x 250 mm for the Pro and 320 x 330 x 380 mm for the Max). Their swappable extruder design allows for standard filaments like PLA, ABS, TPU and PETG with a 1.75mm extruder on the one hand, on the other hand, thermoplastic rubber with a 2.85mm extruder.
Both machines integrate heated build platforms to ensure quality and to prevent warping, as well as a 4.3” LCD touchscreen that eases the preview of print jobs and set printing parameters.
The 3D printer manufacturer believes the processing of TPR filament can open up a range of applications in a wide range of industries. The campaign demonstrates the creation of rubber products, from shoes to sporting goods to medical devices.
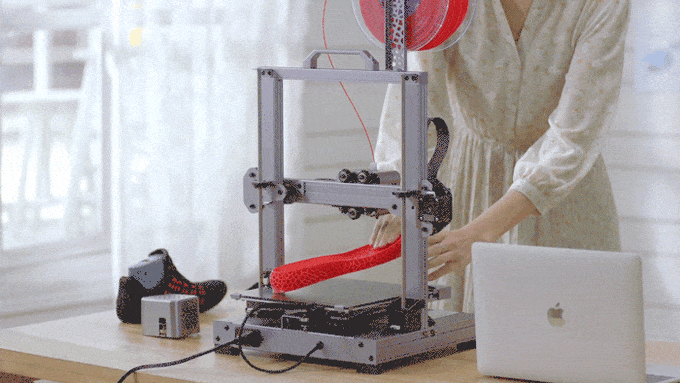
Rubber is still an unusual material in the 3D printing sphere. One of the companies that explores the use of such material is TreeD filament with its PNEUMATIQUE 3D printing filament; a material that derives from recycled rubber tires and offers similar qualities to the original material in terms of strength and flexibility.
In this specific case, Atomstack said they invented “a special rubber filament TPR (Thermo Plastic Rubber) material that has never before been available for desktop 3D printers. This specially designed TPR has properties that make it perfect for 3D printing. With high elasticity (50-70A hardness) and resiliency ( >50%), you can use our TPR filaments to print any end-use rubber products”
“For years, the FDM 3D printing industry has been trying to develop a reliable way to print with rubber-like filaments,” commented Jason Li, Atomstack CEO. “This has been difficult for a number of reasons including the fact that highly elastic filament materials are prone to jamming. To solve these problems, we had to rethink the entire process. We began by designing a new 2.85mm direct extruder design that eliminated nozzle jams, then we developed special rubber filament TPR with a high elasticity (50-70A hardness) and resiliency (>50%) capable of accurately and reliably printing virtually any end-use rubber products.”
Here is the campaign on Kickstarter.
Remember, you can post free of charge job opportunities in the AM Industry on 3D ADEPT Media or look for a job via our job board. Make sure to follow us on our social networks and subscribe to our weekly newsletter : Facebook, Twitter, LinkedIn & Instagram ! If you want to be featured in the next issue of our digital magazine or if you hear a story that needs to be heard, make sure to send it to contact@3dadept.com