We met Annika Ölme during our journey of discovery at Arcam AB Center of Excellence. She brings a decade of industry experience at GE Additive Arcam AB. As Vice President of Engineering, she is responsible for the product development of ARCAM EBM’s machines and the surrounding equipment that supports the machines. A role that is often misunderstood in the industry.
In this Opinion of the Week series, she shares key insights into the mission of a product development manager and how this profile is continuously challenged in an Additive Manufacturing business.
Last but not least, as VP of Arcam EBM, we couldn’t help but explore with her the current applications that are fostering the use of Electron Beam Melting Technology (EBM) in this industry.
First, the role of “Product Manager” is different from the one of “Product development Manager”
In many companies, a product manager fulfils a commercial role where he/she is responsible for the profits and losses of the product line. He/She focuses on the growth strategy around a specific product and concentrates on the user requirements. The product development manager manages the engineering or product development department. He/She does a lot of technical development work and manages the engineers that develop the product.
Are the functions the same in an AM company and in a company that develops traditional manufacturing technologies?
I would say YES & NO.
YES because, the work is similar in terms of what a product development process looks like, the safety precautions that you have to pay attention to, the chain of reasoning that the specialist has to follow.
However, the difference occurs when we are talking about a hi-tech company with technology on its way of maturing, when it is in its “early development stage”. In that specific case, there are more technical duties. You need people that can also go across different engineering principles. In this type of company, an electrical engineer needs to have a broader approach to the job. He/She, for instance, has to understand a bit of physics and mechanical design. My people need to have a much more complexed profile.
So, the leadership challenge is different. In essence, as we are maturing, we are becoming more like an industrial company. We learned from the traditional industry and we are becoming more process-oriented.
During the launch of ARCAM Spectra H, you said, “It’s not a machine, it’s a system”. Could you please elaborate on that?
That’s a statement that is quite important, in my opinion. If you look at the settings of serial production of blades, for instance, the EBM machine is only a very small part of the production workflow. In a nutshell, the operator will need to have a specific powder which once in the machine forms a part. Thereafter, he/she will “depowder” that “powder cake” to take the component out of it. To achieve that, various steps must be followed. It’s only going to be a viable production method if all that flow is automated and works well.
In the same vein, when we launched Spectra L for instance, we simultaneously launched a powder-removal system because it is also part of the production ecosystem of a company that serial-produces parts.
Imagine that you build the perfect Additive Manufacturing machine and thereafter, the next step is only manual, you will not have a viable production.
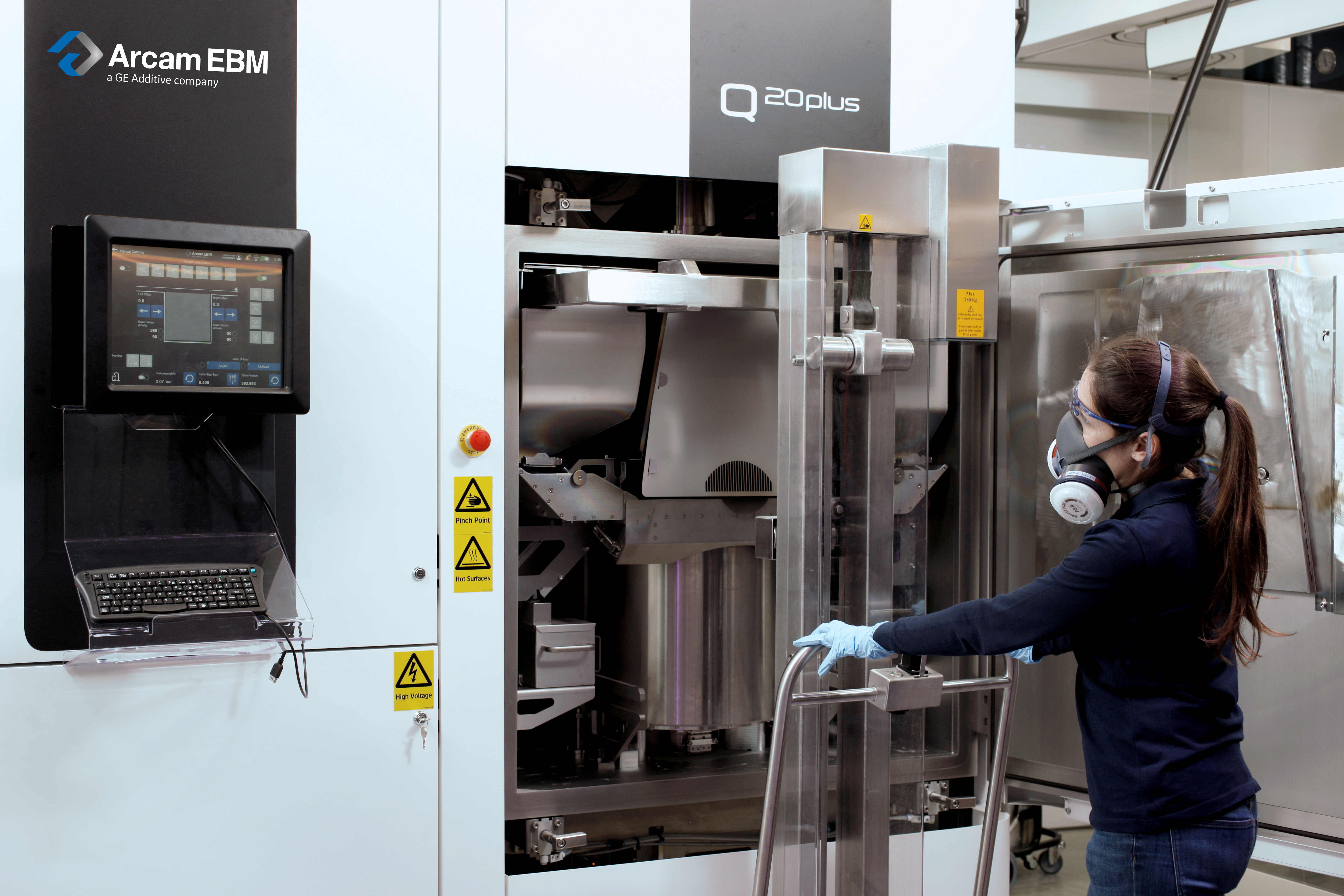
www.gerhard-blank.de www.luftbildmuenchen.com fon: 0049 171 2888481
Let’s talk about interoperability which is still a big issue in AM. What type of issues the user might encounter ? Who experiences it the most ?
It’s all about having a real predictable flow in the whole manufacturing process. What you do before additive manufacturing and after it, before getting to the final part.
Machines are a big part of that challenge, but we can also affirm that it’s software. GE Additive is currently quite involved in this stage of manufacturing by addressing different solutions that will enable users to have a modern production.
Furthermore, it should be noted that R&D experts from universities will not have the same challenges than industrial companies that strive to achieve serial production. In this specific case, the needs are driven by serial producers.
A university that wants to work on material development, for instance, will buy one machine, an Aerospace company which is looking for serial production will buy 100 machines. The gap is very large, the challenges also are.
What are the trendy applications with EBM apart from aerospace and medical industries that are always mentioned?
For this technology to be efficient and cost-effective, you can reach industries that have less expensive materials than they usually use and industries that have a bigger demand for reliability and repeatability.
That means automotive becomes an interesting one to watch. And a couple of trends drive this interest: electrification, for instance, is one trend hence the increasing need for copper additive manufacturing. Due to its conductivity, copper plays a key role in the electrification of vehicles. To take advantage of copper with good conductivity, the material should integrate a low oxygen content but the problem is, copper with very low oxygen level is very hard to manufacture.
In that regard, the nature of EBM itself is a key advantage. It offers very high purity with a very lifted oxygen content. So, this increasing interest in automotive plays to our strengths.
Another interesting application for the future that is worth to note is tool steel, a high carbon alloy steel. That’s the hardest steel one can produce. In the oil and gas industries, this type of materials can be leveraged to produce some parts that wear out very quickly.
Regarding the use of pure copper for automotive applications, a lot of AM technologies also claim to achieve such type of applications. Have you been able to make a kind of comparison with EBM?
It’s hard to see through the various AM technologies. However, the main differences are conductivity and oxygen content.
Anyone can make copper, but the difference will be on the purpose of your application: do you need it to be conductive or not ? For electric parts of vehicles, it’s crucial.
Moreover, the oxygen content will determine whether or not the part will crack. So, if you have a very lifted oxygen in the machine, it becomes very hard that the part cracks.
The third thing I will mention is the business case: productivity. How much does it cost to build the part?
If we look at Laser Beam technology, for instance, it is made out of light, photons. Photons are inherent to Laser Beam technology whereas electrons are inherent to EBM. A very high percentage of laser beam gets reflected away from the copper, more than melting the material, which means that it becomes very unproductive. That’s also the reason why specialists of this technology tend to develop green lasers for this application. However, on the other side, it means that it becomes cheaper to make pure copper more productive with EBM.
Sustainability becomes a key issue in AM. According to you, where is Arcam AB headed?
As far as this issue is concerned, we are very proud because EBM is a green technology itself. It’s much more energy-efficient to produce a part on an EBM system – if you compare with casting for instance -. So, our customers become more environmental-friendly by using our technology.
From the very beginning, we looked at how it could be cost-saving for the user and, in that regard, you are more “environmental-friendly” if you do not use much energy. That’s a value in itself, right? 😊