Arash Motor Company, a UK-based manufacturer of hypercars and sports cars, is utilizing 3D printing in the product development cycle of its next-generation vehicle.
Led by Arash Farboud, founder and lead designer, the company is acknowledged for its boutique, lightweight, high power, and sports cars such as the AF8 Cassini sports car and AF10 electric-petrol hybrid. With a low volume production, Farboud can provide each driver a holistic driving experience and one of the strong production tools that help achieve this vision is 3D printing.
The designer has been using 3D printing for several years now. While we don’t know all the technologies he has in-house, we do know he is an advocate of MakerBot technology, as the MakerBot Replicator 2, Replicator Z18, and METHOD X 3D printers are used for various projects he carries out.
On the other hand, the presence of MakerBot’s technology in this automotive facility is not that surprising when we know the various applications this technology has enabled in the middle of nowhere, or even for luxury automotive and lifestyle brands.
In this specific case, Farboud and his team utilized all three MakerBot 3D printers for a range of applications for the company’s latest electric hypercar project. Built with ultimate performance in mind, the new hypercar comes equipped with a carbon motor cartridge, multiple electric motors, an advanced battery pack, and a sleek aerodynamic design.
The manufacturing process
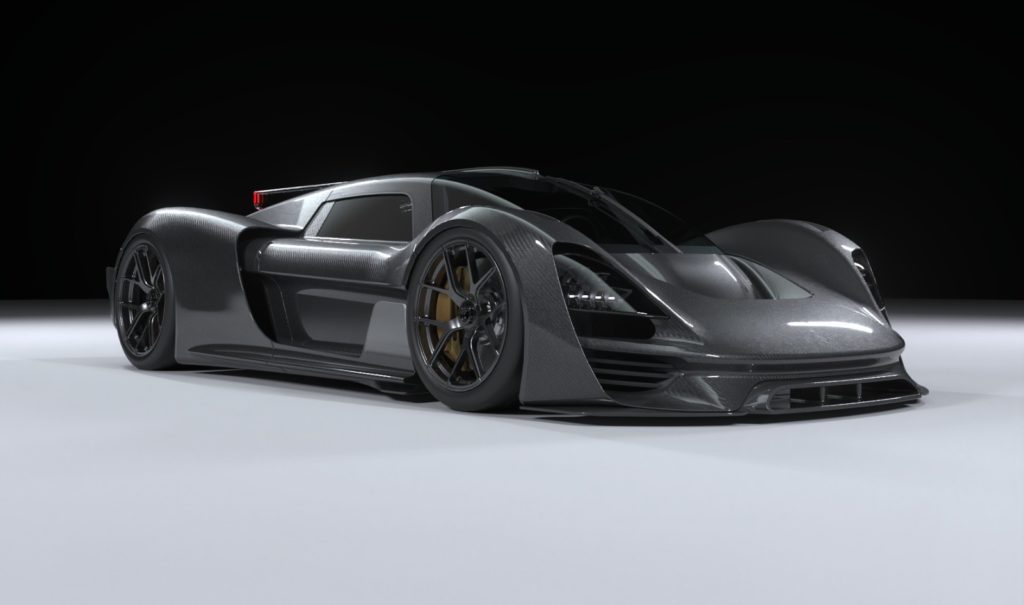
First, it should be noted that their first manufacturing route required to go through the time-consuming and cumbersome process of prototyping with aluminium – from fabricating, bending, welding, shaping, etc.
“The amount of resources needed to do those steps is straining. Once you have a 3D printer to eliminate a lot of those steps, then you’re allowing your resources to be used on things that really matter to you,” the founder explains.
So, the team started with a full-scale model produced using the Replicator 2, thereafter, began to design the complex chassis structure and the aerodynamic structure using the Replicator Z18. This included new techniques like suspension and wing design, wishbone suspension checks, hub and center lock fitments, and scale models to show structural parts.
Using a range of materials on the MakerBot METHOD X, including MakerBot Nylon Carbon Fiber and ABS, the team 3D-printed production parts to be used directly on the vehicle. The METHOD X produced parts in real form, allowing the team to use the parts for stress tests, brackets, gears, and other components for the car.
The hypercar has a lot of complex pieces inside, such as the rear and lower rear wing, so the team had to figure out how to reduce the weight of machining aluminium. To do that, they instead used 3D printed nylon carbon parts.
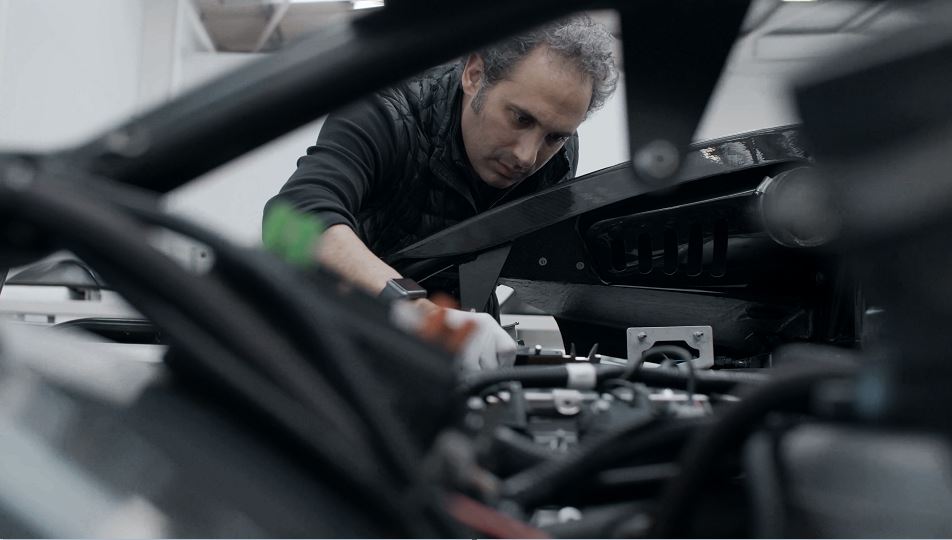
“We’re using a lot of bracketry, fasting points, and fixing points around the car in a 3D-printed nylon carbon fiber. We’re also using a lot of interior structures in ABS and nylon carbon fiber because it’s quicker and easier to make. We’re trying to get 95+% of the car in a composite material to be even higher, and we’re also trying to reduce the complexity of manufacturing to 3D printing. We’re only focusing on the parts that really matter in composite manufacturing – chassis, body panels, some interior structures. We’re deskilling a lot of the processes in some ways and upskilling in other ways for the complexity and accuracy,” Farboud stated.
The team used to send parts out to be machined locally or overseas, which was costly and time-consuming. But now they can send their CAD design directly to the METHOD X to make a part, check it, and test it.
“3D printing in-house also means you can get things done quickly, immediately, and at the lowest cost possible. That means you’re able to experiment without too much fear and worry about spend. You’re just spending money on your filament and your time so that allows you to try things out fearlessly,” he continued.
With three designs from sketch to scale modeling to CAD modeling to fixtures, servicing, and interiors, the team was able to shorten their timeline, which can be up to several years, to 12 months. From that point on, they were able to create a couple of prototype and test vehicles – and then move towards full productization.
“The MakerBot 3D printer series reduces the time from a file on the computer screen to prototyping and checking for touch and feel. That’s a big thing. Sometimes you miss a hole or a fixture, but you can catch that on a CAD model. Then after it’s printed, you can physically check it. The METHOD X has a built-in advantage of having a heated chamber, which is critical for us as it allows for dimensional accuracy. As the part is being made, the base doesn’t move and there is no warping. This allows for high accuracy for a 3D printer of today’s standards. We’ve done several tests and it’s been very accurate each time,” Farboud concludes.
Remember, you can post free of charge job opportunities in the AM Industry on 3D ADEPT Media or look for a job via our job board. Make sure to follow us on our social networks and subscribe to our weekly newsletter : Facebook, Twitter, LinkedIn & Instagram ! If you want to be featured in the next issue of our digital magazine or if you hear a story that needs to be heard, make sure to send it to contact@3dadept.com