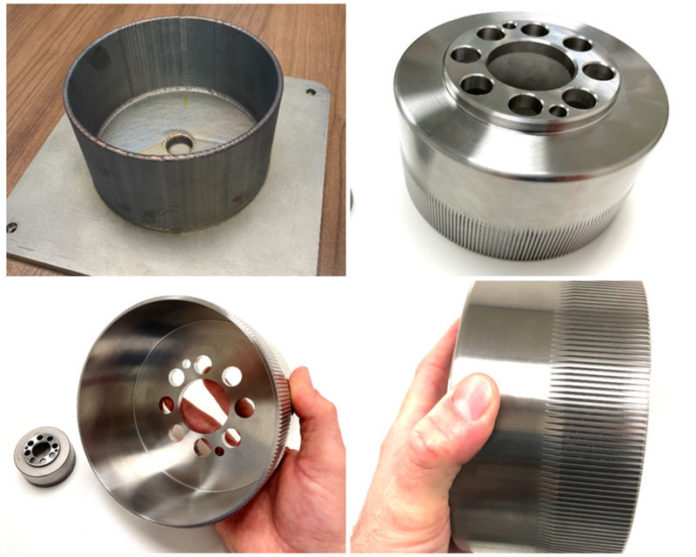
AddiTec, partenaire fondateur et revendeur de l’équipementier d’imprimantes 3D Meltio, travaille avec Amorphology, une spin-off de la NASA spécialisée dans les matériaux avancés, au développement de composants spéciaux de boîtes de vitesses imprimés en 3D.
Les engrenages à ondes de déformation sont des réducteurs compacts et sans jeu utilisés dans les bras robotiques et les mécanismes de mouvement de précision. Ils transmettent le couple par l’intermédiaire d’une coupelle, d’un chapeau ou d’une bande à paroi mince, appelée flexspline. Le flexspline possède des dents d’engrenage précises et une paroi flexible, une combinaison de qualités qui fait baisser les coûts de fabrication d’un réducteur à ondes de contrainte. En raison de leur complexité, les engrenages à crémaillère peuvent représenter une part importante du coût d’un bras robotique à six degrés de liberté (6DOF).
« Lorsque vous envisagez l’usinage de flexsplines de 6 à 8 pouces de diamètre, la grande charge d’acier peut être réduite à seulement 10 % de son volume d’origine. Cette situation est préjudiciable du point de vue des coûts et du développement durable, car de l’énergie et des matériaux sont gaspillés pour produire une pièce qui n’est qu’une coquille du matériau d’origine. La fabrication additive devient une alternative prometteuse puisque les coûts d’usinage peuvent potentiellement être réduits de façon spectaculaire tout en permettant l’utilisation rentable d’aciers à haute performance », a déclaré le Dr Glenn Garrett, directeur technique d’Amorphology.
Ensemble, Amorphology et AddiTec ont fait la démonstration d’un prototype de 6 pouces de diamètre d’une flexspline d’engrenage à ondes de déformation imprimée dans un acier haute performance 17-4 trempé par précipitation. Le prototype a été fabriqué sur un système hybride CNC Haas utilisant le moteur Meltio. La pièce imprimée a été retirée du plateau de montage, puis usinée par CNC pour obtenir la forme de précision. Le processus permet également une production flexible et ponctuelle d’une variété de flexsplines de grande taille sans avoir à conserver en stock de nombreux diamètres.
« AddiTec utilise la technologie de dépôt de métal par laser avec fil et/ou poudre (LMD-WP) de Meltio (une forme de DED). Dans le processus LMD-WP, les lasers créent un bain de fusion dans lequel on introduit du fil et/ou de la poudre pour créer des cordons de soudure. Ces cordons de soudure sont ensuite superposés avec précision pour fabriquer des composants métalliques de forme quasi nette. Cette technologie peut être utilisée pour créer des composants à partir d’une conception CAO ou pour réparer des pièces. En outre, sa capacité à s’intégrer à une machine CNC en fait un système hybride. La fabrication hybride est une « solution unique » pour la production de composants métalliques sans soudure – elle combine les opérations additives et soustractives sur une plateforme commune, réduisant ainsi le coût global et le temps de fabrication des composants », explique Brian Matthews, CEO d’AddiTec.
N’oubliez pas que vous pouvez poster gratuitement les offres d’emploi de l’industrie de la FA sur 3D ADEPT Media ou rechercher un emploi via notre tableau d’offres d’emploi. N’hésitez pas à nous suivre sur nos réseaux sociaux et à vous inscrire à notre newsletter hebdomadaire : Facebook, Twitter, LinkedIn & Instagram !