The company is now open to licensing its technology.
OEM AIM3D increases protection for its technology in the USA and Europe with patents granted in the field of compact decentralized pellet extruders and material extrusion printing. The US patents also cover filament extruders (FDM printers) for high-temperature applications and high-flow hot ends.
Since 2017, the spin-off from the University of Rostock (Germany), has been consistently focusing on 3D pellet printers. Significantly lower material acquisition costs for pellets and the inline recycling of reclaimed material form the basis for the high cost-effectiveness of this AM production strategy with 3D pellet printers.
The development work on 3D pellet printing technology was reflected in four patent applications between 2016 and 2018, which have now been granted in 2023. The patents protect both the topology of the 3D printing extruder as a whole and detailed technical solutions in the area of pellet processing.
An overview of the patents
The patents granted are published as EP3463799B1, EP3648946B1, US11541593B2 and US11597118B2. EP3463799B1 (application: 27th May 2016) is entitled: “System for the additive manufacture of metal parts”. EP3648946B1 (application: 26th June 2018) relates to: “Compact extruder and extrusion of thermomechanically deformable pellets”. Patent US11541593B2 (application: 27th May 2016) is entitled: “Extruder for a system for the additive manufacture of metal parts using the composite extrusion modeling (CEM) method”. The US patent US11597118B2 (application: 26th June 2018) defines: “Device and method for the extrusion of thermo-mechanically deformable materials in bulk form, and compact screw extruder”. The four patents include the priorities of two original German patent applications and some of them date back to the time before AIM3D was founded.
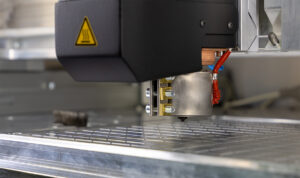
Significance of these patents
The thermal separation of the housing and the division into an actively cooled and a heated area of AIM3D’s CEM technology lead to a short melting zone and uniform extrusion at high build rates (based on nozzle sizes of 0.3 mm to 0.6 mm). AIM3D has positioned its technology in this market segment and thus differs fundamentally from large-capacity pellet printers that rely on nozzle diameters larger than 1 mm. This becomes particularly evident in the processing of ULTEM 9085, a material that is of great importance in the aerospace sector, which can be processed by AIM3D’s patented pellet extruders in a material-friendly and reliable manner with high build rates and very good surface quality. The design of the extruder guarantees a short melting zone, which prevents degradation of the material, which would inevitably lead to process fluctuations and weak points in the components. In combination with the active filling of the extruder’s feed area, this ensures a uniform static and dynamic pressure in the extruder, which in turn leads to uniform extrusion widths and therefore a high component quality. Beyond the processing of metal-filled composites (as mentioned by name in the patents), the system-specific patent claims also extend to the processing of thermoplastic polymers, as long as the system-specific elements are found in the systems and the processing of metal-filled composites (for example, MIM material) cannot be technically excluded.
The US patent US11541593B2, “Extruder for a system for the additive manufacture of metal parts using the composite extrusion modeling (CEM) method”, describes the topology of the thermal separation. In addition to the use of pellets, which are fed into the melting unit via a screw, it expressly includes the use of sticks or filaments, which are advanced via drive wheels. In principle, the protection of the US patent thus also applies to hot ends and extruders of filament or stick-based systems that use thermal separation in the melting unit, for example, in order to achieve higher flow rates or for the processing of high-temperature materials.
Remember, you can post job opportunities in the AM Industry on 3D ADEPT Media free of charge or look for a job via our job board. Make sure to follow us on our social networks and subscribe to our weekly newsletter : Facebook, Twitter, LinkedIn & Instagram! If you want to be featured in the next issue of our digital magazine or if you hear a story that needs to be heard, make sure to send it to contact@3dadept.com