Did you know that nuclear energy provides about 10% of the world's electricity from about 440 power reactors? Surprisingly, it is the world's second largest source of low-carbon power (28% of the total in 2019). The thing is, the construction of new reactors has been stalled across the world – since the 1990s in fact – and this is due primarily to the competition with other means of energy.
While many operating reactors are facing retirement, high initial capital investment limits the utilities to build new large reactors generating electricity via the steam cycle. To maintain the nuclear share in the energy portfolio, there are strong interests in smaller, simpler, and more efficient nuclear power units for generating electricity and processing heat. A number of advanced reactor concepts, including small modular reactors (SMR) and GEN IV advanced reactors (e.g., sodium metal fast reactor, molten salt reactor, gas-cooled reactor), are under consideration.
To support the deployment of these advanced reactor designs, the nuclear industry is looking for new ways to manufacture nuclear components for plant construction, reactor internals, fuel claddings and assemblies, sensors, and instruments and to reduce the overall cost and deployment time.
Our bet is that additive manufacturing might be one solution to explore here. But what are the risks and challenges?
This is the focus of our next additive talks session. Set to take place on Wednesday 11th May, 2022 from 09.30 am to 10.30 am Cambridge, Massachusetts Time (03.30 pm to 04.30 pm CET), the virtual table will host two main stakeholders:
Dr. Benjamin R. Betzler is a senior R&D staff member at Oak Ridge National Laboratory and group leader of the Research and Test Reactor Physics Group. He joined the laboratory in 2014 after completing his Ph.D. in nuclear engineering and radiological sciences at the University of Michigan. His research focuses on advanced reactor design and Monte Carlo radiation transport methods.
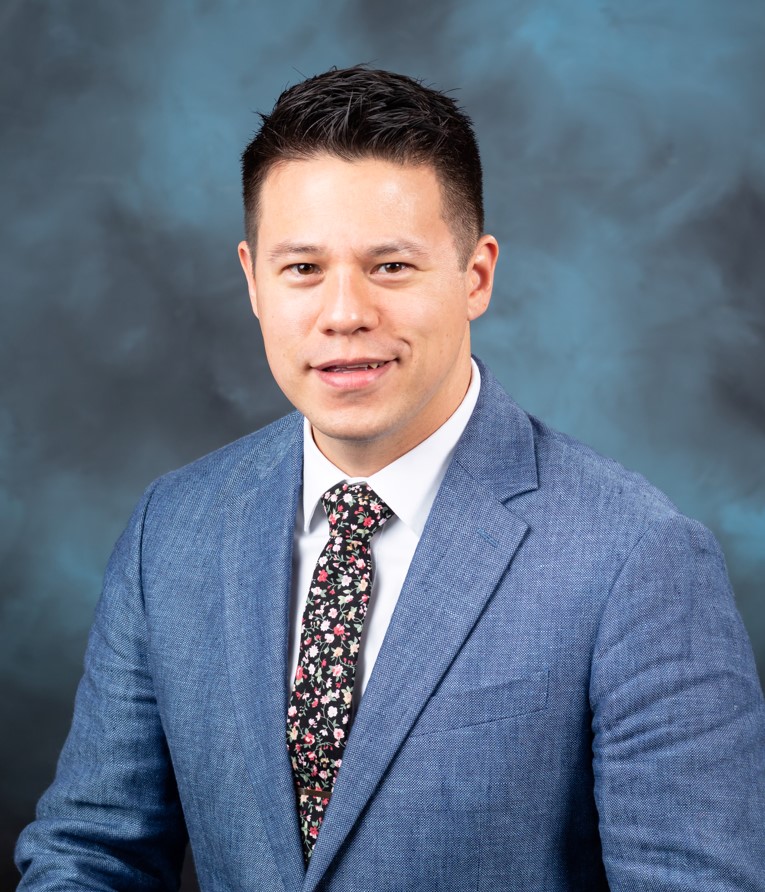
ORNL's mission has grown and expanded through the years, and now it is at the forefront of supercomputing, advanced manufacturing, materials research, neutron science, clean energy, and national security. With 4,200 staff, 3,000 guest researchers, 20 user facilities, and a budget of approximately $1.2 billion, ORNL supports the Department of Energy's mission through six major scientific competencies in energy, neutron science, high-performance computing, complex biological systems, materials research, and national security.
Yevgeni Brif has over a decade of experience in materials engineering, with a focus on heavily regulated industries. He joined Burloak Technologies in 2019 as Additive Manufacturing Process Engineer and moved into the role of Program Manager in 2021. In his current role Yevgeni develops business opportunities with customers and leads the planning and implementation of complex projects in alignment with customer expectations. Prior to joining Burloak, Yevgeni was a Metal Additive Manufacturing Researcher with the University of Sheffield. He holds a master’s degree in Advanced Metallurgy from the University of Sheffield, a Bachelor of Science in Material Engineering from the Technion – Israel Institute of Technology and is a member of Professional Engineers Ontario.
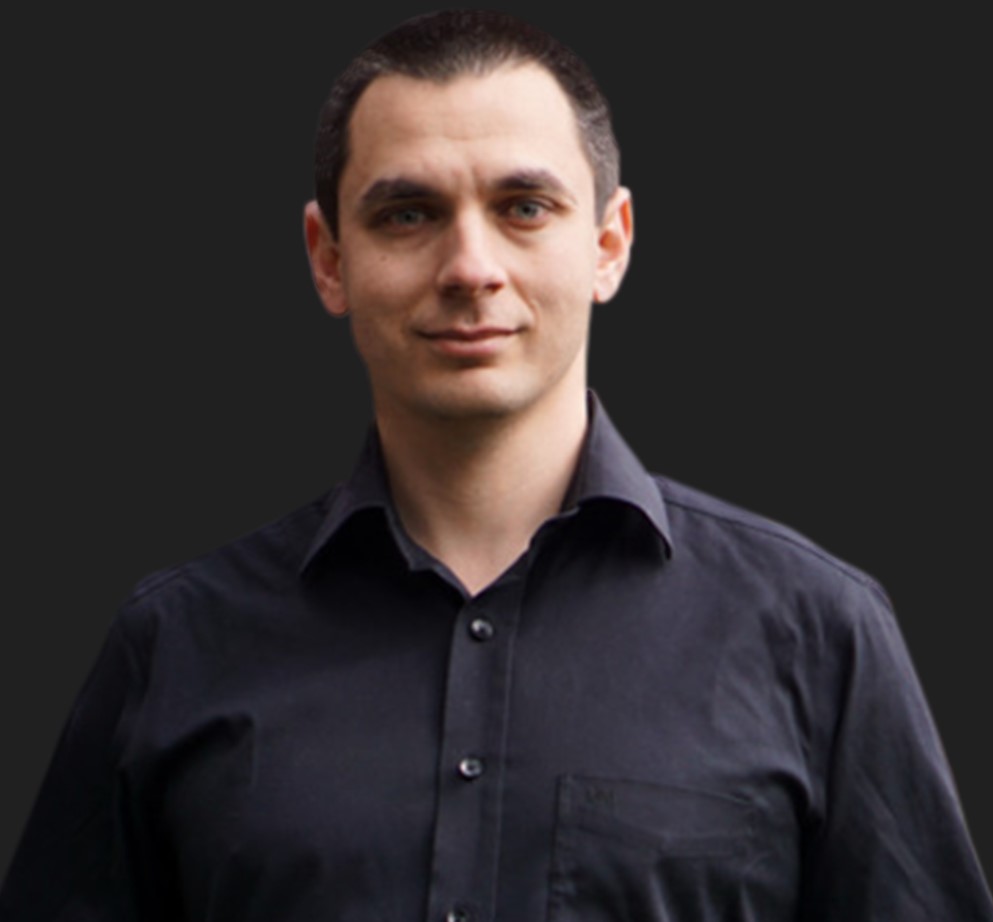
Burloak Technologies, is an additive manufacturing company which is part of the Samuel Group. The company provides engineering and design services for additive manufacturing, materials development, high precision CNC machining, post-processing and metrology. Burloak works with the most innovative companies in the space, aerospace, automotive and industrial markets to rapidly transition their most challenging part designs to be additively manufactured at scale. The Company is registered to AS9100D, ISO9001 and is Canada Controlled Goods Approved.
Do you want to be part of this conversation?
Interestingly, during this session, we will have a special guest who will challenge the insights of those industry insiders. Don’t get us wrong, the audience’s questions are always welcome. However, Iwan Grech, our special guest, brings here competences in both sectors of activity (AM and Nuclear), therefore will bring relevant questions that may help the audience better understand this topic.
Whilst undertaking his Physics degree, Iwan Grech discovered that utilising nuclear energy would be key in reducing global emissions and tackling global warming on a large scale. This led to Iwan attaining a master degree in Nuclear Energy, with a focus on the materials used in nuclear fission and fusion plants where he worked on a project at Culham Centre for Fusion Energy (CCFE). It was during the masters’ programme that Grech first became aware of Additive Manufacturing (AM) and the manufacturing techniques potential to reduce waste and allow for rapid product development. Following his masters, Grech has just completed his PhD in the mechanical and corrosion performance of additively manufactured stainless steels.
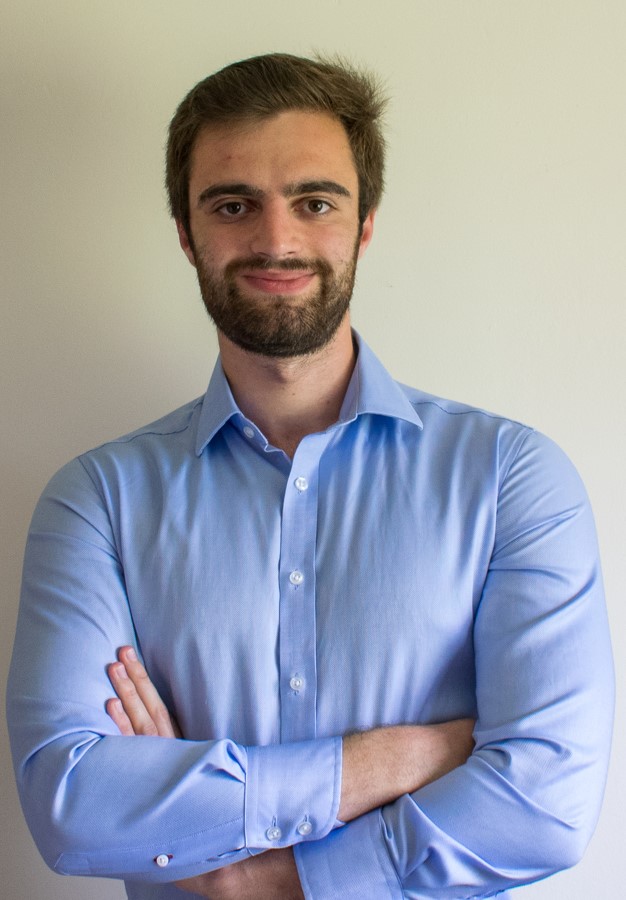