3D printing is being applied in almost all industries. Who knew that large 3D printers could even be used in printing houses, automotive and aeronautical components, footwear, as well as medical implants?
Not all 3D printing materials are capable of printing these designs, and in this article, we’re going to explore ABS and ASA materials being used in large format 3D printing.
But before we have a look at that, let’s learn about large format 3D printing.
What is large format 3D printing?
Large-format 3D printing is the printing of large objects that were traditionally machined or molded. In other common 3D printing, a large object can be printed in sections then later those parts are combined together, but with large format 3D printing, the entire object is 3D printed using large format 3D printers that are available now, some even with the capacity to print volumes of up to 1M3. A good example of a large-format 3D printer is the Extreme Builder 2000 Pro, Bodix Big- 120X, and also BigRep Studio G2.
Having learned what large-format 3D printing is, we would like now to learn about the technologies being used in large format 3D printing.
Technologies used in Large Format 3D printing
- Fused Deposition Modeling (FDM): A common 3D printing technology being used in the 3D printing world. It was developed by S. Scott Crump in the late 1980s. Stratasys later commercialized it in 1990. FDM works by creating an object by extruding plastic on the build plate layer by layer. This technology works well in most large 3D printers.
- Stereolithography: is another technology used in large scale 3D printing. Stereolithography produces models by using the polymerization principle where UV-sensitive resin is utilized. When this technique is used, it’s always recommended to use isopropanol to clean the room in order to remove the non-solidified resin. UV post-treatment is also required to make the material stronger. SLA prints complex models by the use of scaffolds and they are removed during the post-processing process.
- Digital Light Processing (DLP): A 3D printing technology that is similar to Stereolithography. The difference is that DLP uses crystal display panel liquid. It also uses a different light source that is controlled by micromirrors.
Those are just but some of the technologies that can be used in large format 3D printing. There are also other technologies like Selective Laser Sintering and Selective Laser Melting.
Having looked at the technologies, we would like now to look at the ABS and ASA materials.
ABS Material
ABS standards for Acrylonitrile Butadiene Styrene. ABS is an amorphous and an opaque thermoplastic polymer. These materials can be heated above their melting point and they don’t degrade. Instead of burning when heated. It instead turns into a liquid and this makes it easier to be recycled and even injection-molded when used in the Injection. As mentioned above, ABS is amorphous. This means that it doesn’t give crystalline solid order characteristics when heated.
ABS is offered by many companies as filaments. Examples of the supplies of ABS include the Stratasys, Esun, Formfutura, and also Ultimaker. Though these materials are mostly used in the additive manufacturing industries, it’s also a resin that has the same mechanical properties as the ABS and is used in Stereolithography.
How is ABS Made?
ABS is made through the process of emulsion. This is where a mixture of various products that don’t necessarily combine into one product are mixed together. Though there are other processes used in creating it like mass polymerization where styrene and acrylonitrile are polymerized in the presence of polybutadiene, the emulsion process is the most common.
In addition to the above, ABS is also usually created through the recycling of other ABS plastic as it’s a thermoplastic material.
Properties of ABS that Makes it a Good for Large Scale
- Toughness and impact resistance: This makes ABS be a great material used in mechanical designs. The toughness and heat resistance can also be increased by increasing the polybutadiene proportions in relation to acrylonitrile and styrene.
- Very strong and durable: They can be used to produce really strong components that can last for long.
- ABS is resistant to alkalis, aqueous acids: This makes it much useful in the injection molding processes and 3D printing in the FDM 3D printers.
- It’s Cheap: It’s the cheapest of all the 3D printing materials and that’s why many 3D printing communities prefer this material.
- ABS can easily be sanded: Once the model has been 3D printed with ABS, one can smooth it and jagged edges can also be removed without much difficulty. Parts that are broken during the 3D printing process can also be repaid and glued easily.
- ABS can be recycled: This makes production easier.
- Little post-processing required: After 3D printing, ABS doesn’t require a lot of post-processing activities. This is advantageous as it saves time more so when 3D printing complex parts.
- It also has great electrical insulation properties
- Good weldability
- Excellent surface aspect and high surface brightness
- Good insulating properties
- High rigidity
All the above properties are attained during the initial creation processes of ABS.
If one requires an inexpensive, still, and strong 3D printing material that endures external factors, then ABS is a good choice. ABS should also be kept in a dry place as it absorbs moisture.
Where is ABS Used at?
ABS is used in various fields. These includes:
- Automobile industry:
- Consumer products
- Pipe fittings
- Used in making lego toys
ASA Material
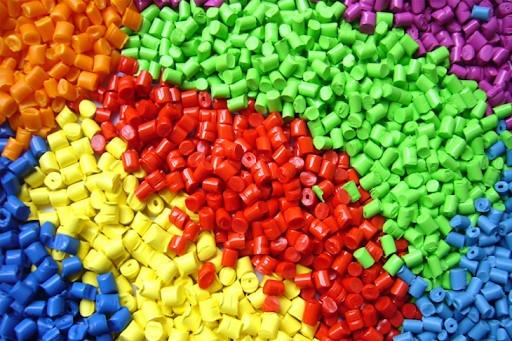
ASA material stands for Acrylonitrile Styrene Acrylate. It was first introduced in 1970 by BASF. The reason why this material was designed was to have a similar material as ABS but with more weather resistance. These features make ABS to be mostly used in the automotive field and other outdoor applications.
How is ASA Made?
ASA is created by the production of acrylic ester elastomer that is grafted during the reaction between styrene and acrylonitrile. Acrylonitrile has great properties like good chemical reactions, toughness, thermal stability, and outstanding resistance to weather and aging.
Properties of ABS that Makes it a Good for Large Scale
- Stable FDM material: that is also very strong and it’s ideal for outdoor applications. That is, from automotive parts to electrical housings as well as sporting goods.
- UV resistant: This makes it great for creating all-purpose prototypes.
- High heat and impact resistance.
- General-purpose and high gloss
In addition to the above properties, all the features of ABS are also found in ASA.
Where is ASA Uses
- Outdoor applications
- Automotive industry
- Electronic/electrical applications
- Useful in garden and lawn equipment
Remember, you can post AM job opportunities for free on 3D ADEPT Media or look for a job via our job board. Make sure to follow us on our social networks and subscribe to our weekly newsletter: Facebook, Twitter, LinkedIn & Instagram! If you want to be featured in the next issue of our digital magazine or if you hear a story that needs to be heard, make sure to send it to contact@3dadept.com