Airbus Defence and Space collaborated with 3D Systems to realise the first 3D printed radio frequency (RF) filter, ready for use in commercial telecommunication satellites.
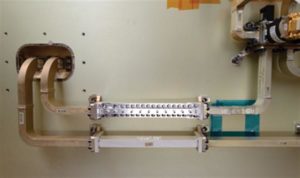
It’s been 50 years that first filters were set up to allow frequencies between one channel and another one. However, the challenge nowadays lies in the capacity to increase multiple beams within a single satellite.
A satellite such as the Eutelstat KA-SAT for instance comprises about 500 RF filters and over 600 waveguides. That’s why, in order to deal with specific frequencies, RF filters are custom-designed.
New design innovation
Through this project, both teams show the capacity to create new design innovation for aerospace parts.
Indeed, they create this RF filter from libraries of standardized elements (rectangular cavities and waveguide cross-sections). Milling and spark eroding techniques were used to build shapes and connections.
That’s why, via two halves bolted together, cavities for RF filters must be machined, requiring by this way extra production time as well as quality assessment.
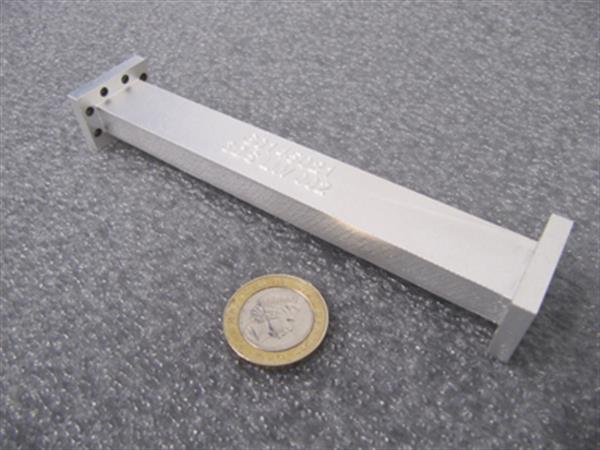
“The disruptive innovation lies in the fact that pure functionality, not manufacturability, now determines how the hardware will be designed,” says Koen Huybrechts, project engineer for 3D Systems in Leuven. “This project is a classic example of ‘form follows function’.”
If mass, cost and time are the main benefits of this operation, notice is to be made that it does remove some concerns.
“The spherical shape of the powder particles used in 3D metal printing lead to a certain waviness rather than steep transitions,” says Huybrechts, “but the ability to shape a part for more effective signal filtering more than overcomes any concerns with surface topology.”
For further information about 3D Printing, follow us on our social networks and subscribe to our newsletter!
//pagead2.googlesyndication.com/pagead/js/adsbygoogle.js
(adsbygoogle = window.adsbygoogle || []).push({});