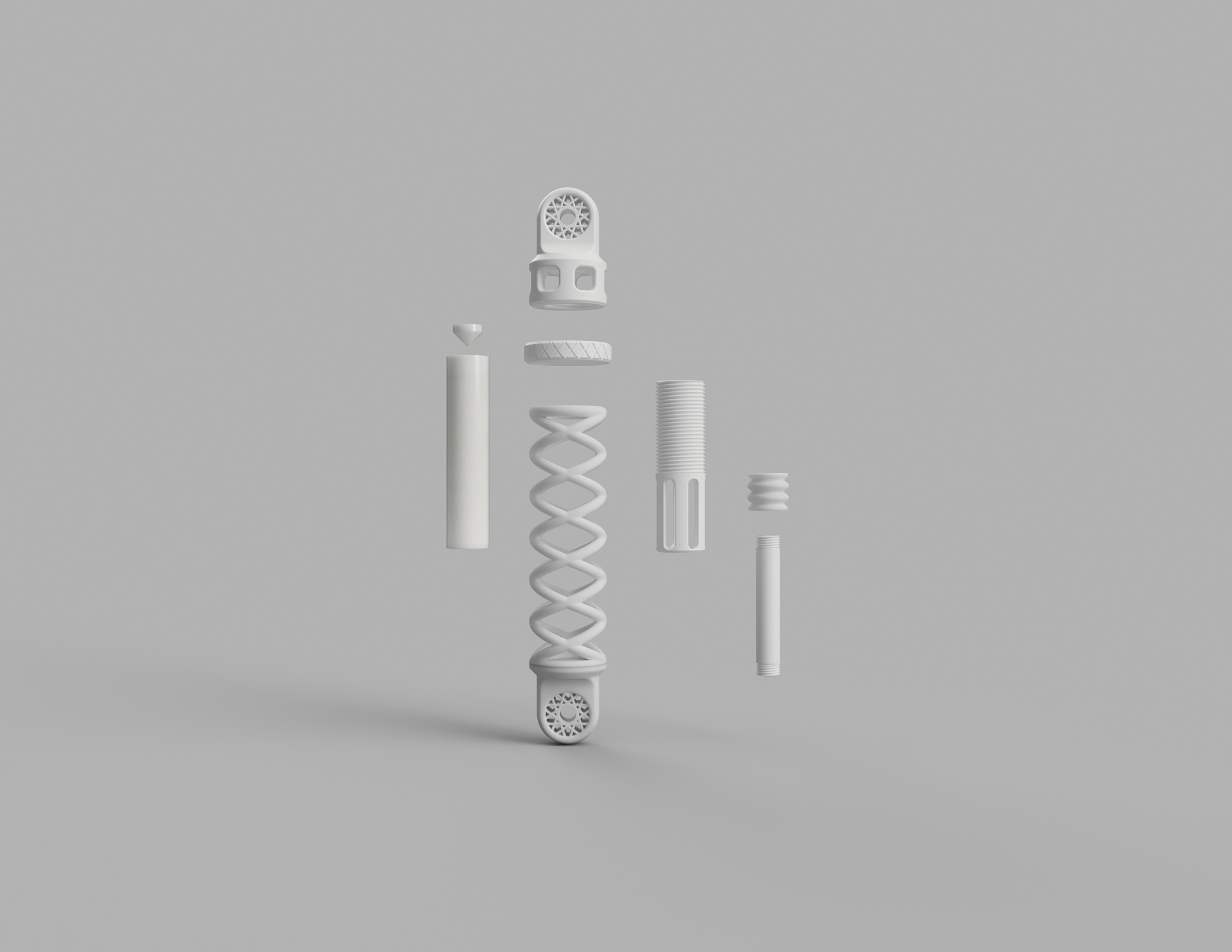
Given their different properties, the filaments, powders and liquid raw materials can be used for a variety of applications. However, it’s quite hard to combine two or more materials in order to manufacture a part.
Covestro, the specialist in polymer materials for 3D Printing, marks a milestone in the creation of individual prototypes with a shock absorber.
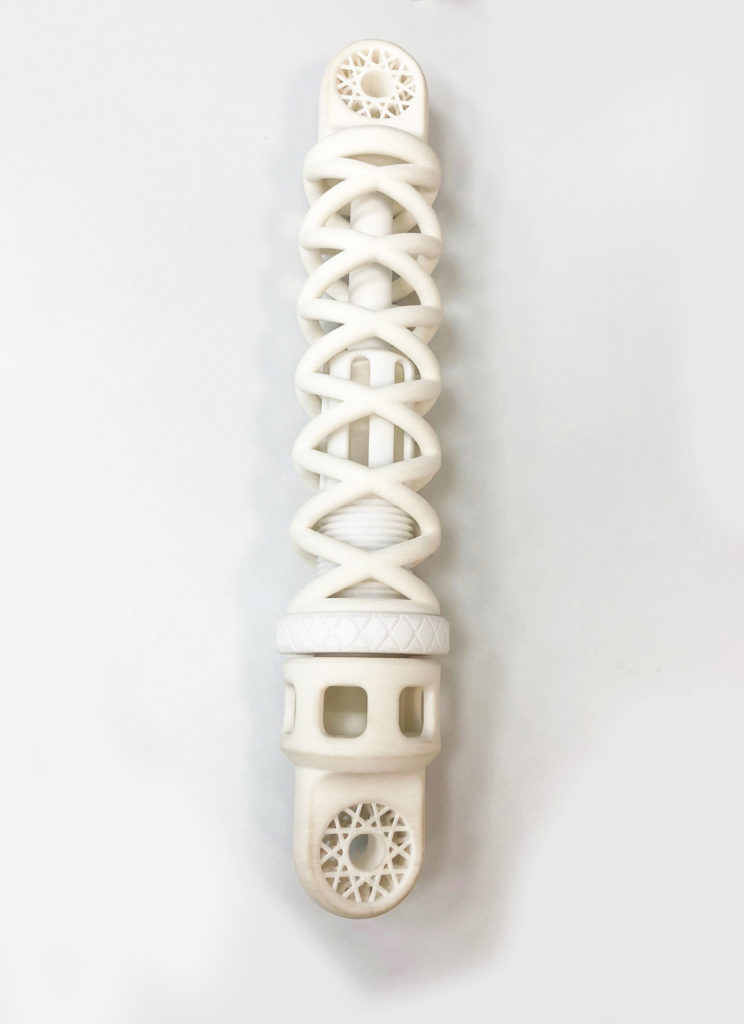
At the Fakuma 2018 trade fair, Covestro will be presenting a complex shock absorber which was manufactured using 3D printing.
The use of different processes & different materials during the production
The most important feature of the shock absorber is the production of individual parts from three different products using three different manufacturing processes.
Let’s take an example of the production of an individual prototype:
The outer spring of the 40 x 7 cm part is made of powdered thermoplastic polyurethane (TPU). It was shaped layer by layer using SLS. It is recognized for its elasticity and high abrasion resistance.
The adjusting screw inside the shock absorber has to be very strong and hard. That’s why, the company used one of its robust polycarbonate materials with the FDM process.
The air chamber in the interior is created from a liquid polyurethane resin. The digital light processing method has proven itself for such components with filigree structures – as in this case as well.
However, it should be noted that when combining different materials, the individual components are subsequently connected to each other. “This complex structure would not have been possible with conventional production processes,” explains Lukas Breuers, marketing manager for 2D and 3D printing at Covestro. “Another new development is the combination of different materials with various, tailor-made properties. This has enabled us to significantly expand the possibilities of additive production and its areas of application.”
Lastly, according to the company, its other 3D printing products are characterized by good heat resistance, abrasion resistance or flexibility.
For further information, follow us on our social media and subscribe to our newsletter!
Would you like to be featured in the next issue of our digital magazine? Send us an email at contact@3dadept.com
//pagead2.googlesyndication.com/pagead/js/adsbygoogle.js
(adsbygoogle = window.adsbygoogle || []).push({});