ABS might be one of the most popular 3D printing materials in manufacturing, but it is also said to be one of the toughest to 3D print on a Desktop 3D printer. The reasons for this lie in the material’s ability to shrink, warp, curl, or crack without the appropriate conditions. Yet, this engineering-grade material can be sanded, finished, painted, and used in real world applications for end-use components – all of this making it a material of choice for several industries and applications from manufacturing tools to production parts.
With the goal of enhancing the production with this material, 3D printer manufacturer MakerBot has been developing a solution that aims to streamline the workflow steps and reduce the need for additional equipment and costs. As observed with almost all the solutions the Stratasys company has unveiled since the beginning of the year, this new solution, MakerBot RapidRinse™, has been designed with METHOD X® and METHOD X Carbon Fiber 3D printers in mind.
The MakerBot RapidRinse™
RapidRinse is a patent-pending, fast-dissolving support material designed to remove cumbersome and expensive post-processing tasks. The company explains that the solution easily dissolves in warm tap water and does not need caustic chemicals as is often the case with some soluble support materials – leaving behind minimal residue. MakerBot states that without the need for solvents, engineers no longer need to purchase additional post-processing equipment.
The support material would deliver exceptional results if combined with ABS-R, a new ABS formulation that enables to achieve “superior printing reliability and performance for consistent, repeatable ABS” 3D printed parts.
Furthermore, from a manufacturing standpoint, let’s remind that with a heated chamber made from a patented VECT™ (Variable Environmental Controlled Temperature) 110 Technology, users of the METHOD X who decide to leverage RapidRinse as part of their production, could achieve ABS parts of ±0.2mm (±0.007 inch). The MakerBot team has already been able to achieve these results internally following testing of certain geometries.
Additional testing at 3D ADEPT Media
Exercise performed by Martial Y. from 3D ADEPT Media.
We can now testify to these results as MakerBot invited us to try the new RapidRinse for ABS by ourselves.
We washed the 3D printed parts we received from the manufacturer in two large bowls filled with warm tap water.
After dropping the ABS-R (red part) and RapidRinse into one container and the PLA (Black) – PVA print into another, we realized after about 1h30 that the RapidRinse material was mostly dissovled compared to the PVA.
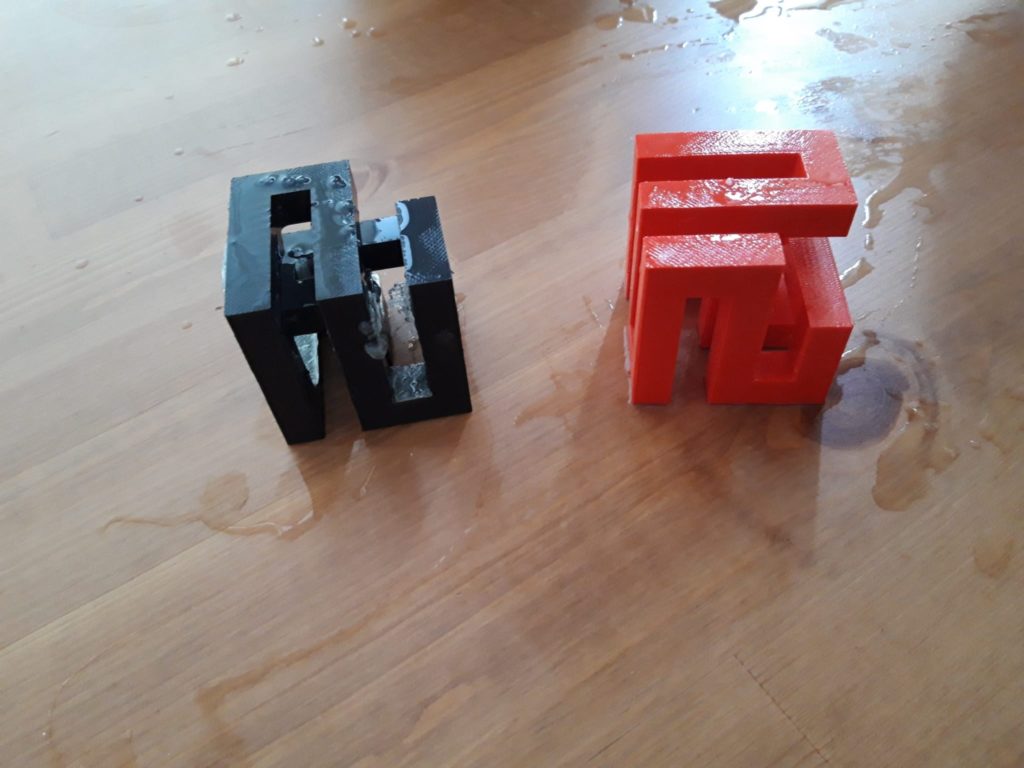
The end of the testing reveals that the thickness of the maze columns is within ffl 0.2 mm – which is exactly what MakerBot announced following testing in their facility.
With the ability to print today polymers, composites, and metals, the MakerBot METHOD X integrates environmental control features that enable its engineering-grade materials to deliver standards required in manufacturing industries. Not to mention that its 6-in-1 modular extruder platform facilitates change between material groups, and prevents cross-contamination as well as rapid extruder degradation.
Last but not least, we are very far away from MakerBot’s ability to print real ABS along with SR-30 soluble supports. With the RapidRinse solution combined with ABS-R, the manufacturer is going one step further, by unveiling the capabilities of a heated chamber to deliver parts with no warping and cracking, and most importantly, parts that meet industry safety standards.
Remember, you can post free of charge job opportunities in the AM Industry on 3D ADEPT Media or look for a job via our job board. Make sure to follow us on our social networks and subscribe to our weekly newsletter : Facebook, Twitter, LinkedIn & Instagram ! If you want to be featured in the next issue of our digital magazine or if you hear a story that needs to be heard, make sure to send it to contact@3dadept.com