Those who are familiar with the additive manufacturing industry or who faithfully follow the latest news of the industry via 3D Adept Media certainly know that Desktop Metal keeps addressing challenges of speed, cost and quality via its metal 3D printing solutions.
The company was present at Fomnext last week and showcased a wide range of developments and applications across industries. We had the opportunity to meet one of the company’s collaborators: Larry Lyons. In addition to being Vice President Product at Desktop Metal, he is a straightforward and friendly guy.
During our talk, Larry Lyons confided in 3D Adept that most of their conversations with their clients start by a single concern: “Can you save me money without having to redesign my parts?”
The company therefore looked for a wide range of solutions that might best address this issue and the latest solution that they will be able to provide a selected group of customers in Q1 2019 is the Production System.
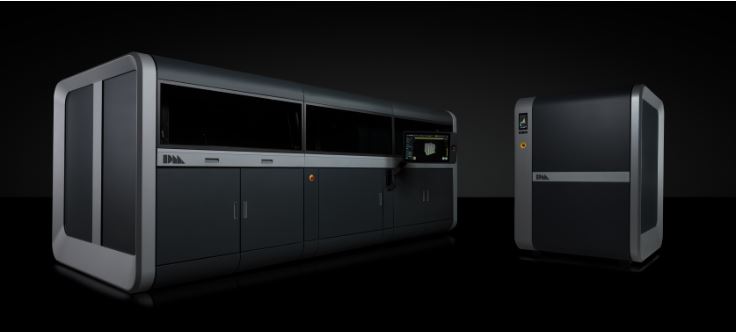
The Production System
The metal 3D printing system integrates Single Pass JettingTM technology and is intended for mass production. According to Larry, the system truly competes with conventional manufacturing processes in terms of speed, cost per part and even build volume.
Indeed, Larry explained that the previous system has a build envelope of 33x33x33 cm, which has been improved in this platform by a build envelope of 75x33x25 cm. Furthermore, “we have gone from 8000 cm3/ hour to 12,000 cm3/hour”, said Larry, speaking about the print speed. In other terms, the system offers a 50% increase compared to the V1.
As far as quality and cost are concerned, the Vice President took an example of a part has been made for decades through traditional manufacturing processes. The part has a complex shape and required a lot of time and cost for the fabrication. Using the Production System, engineers had been able to turn the 20 different steps of the traditional process into 4 steps (combined with much shorter post processing steps of course), therefore they have been able to deliver 20% cost saving using metal 3D Printing.
This is just an example. The main aim is not necessarily to avoid redesigning parts, but above all to meet a set of needs that necessarily include cost, speed and quality. Desktop Metal through the voice of their VP Product, aims at outline the difference between their platform and the ones that are currently available on the market. Indeed, systems might look alike but do not have the same capabilities.
Apart from these features, it should be noted that the platform can be used with inkjet nozzles that enable the printing of a set of metals including tool steels, low alloy steels, titanium, and aluminum at a rate of 3 billion drops per second.
After its first installation at a Fortune 500 company in Q1 2019, the system will be installed at leading automotive and metal parts manufacturers throughout 2019. A broad availability will follow in 2020. And at that moment, we will be able to get an answer to one question that will remain in our minds: “Desktop Metal customers would have really saved money using the Production System without having to redesign their parts?” #StayTuned
For further information about 3D Printing, follow us on our social networks and subscribe to our newsletter!
Would you like to be featured in the next issue of our digital magazine? Send us an email at contact@3dadept.com
//pagead2.googlesyndication.com/pagead/js/adsbygoogle.js
(adsbygoogle = window.adsbygoogle || []).push({});