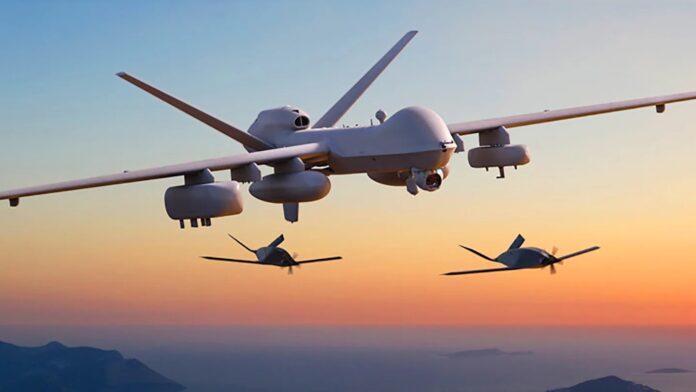
With millions of dollars already saved in tooling, General Atomics Aeronautical Systems, Inc. (GA-ASI) shares the lessons-learned of their journey with industrial Additive Manufacturing. A meaningful example of their story relates to the completion of a lamination mill fixture production achieved in collaboration with Thermwood that led to $50,000 in cost savings.
When you’re a trade press covering the Additive Manufacturing industry, one of the milestones you are eager to see from adopters is the completion and/or installation of a production part within their operations. At that moment, you tell yourself: “We are reaching a tipping point. We are getting there, slowly but surely. It’s a dream come true.” We witnessed that moment for General Atomics Aeronautical Systems, Inc. (GA-ASI) in 2019 when the company successfully flew its first metal 3D printed component; a NACA inlet made of Titanium Ti6AI4V on an MQ-9B SkyGuardian Remotely Piloted Aircraft (RPA). While this was some of the first few milestones we witnessed, it turns out that the company’s activities with AM had started nearly a decade ago and it took a conversation with Steve Fournier to understand the whole journey leading to it.
If you’re new to this space, please note that General Atomics (GA) is a defense and diversified technologies company that develops a wide range of products such as energy systems and unmanned aircraft systems. While AM is leveraged across several GA divisions, the adoption of the technology is largely fostered by GA-ASI. GA-ASI is a prime contractor to the US Department of Defense (DoD), and is best known for the design and manufacture of unmanned aerial vehicles and radar systems. Steve Fournier who shares the company’s experience with AM today is a Sr. Manager at GA-ASI’s Additive Design & Manufacturing Center of Excellence.
GA-ASI’s journey in AM started in the early 2010s when the company decided to explore the use of AM for RPA applications. Before investing in a specific AM technology, the company’s engineering teams worked on various projects conducted in collaboration with machine manufacturers and AM service bureaus. This way, they could learn more about the capabilities of each technology and materials before bringing them in-house. They onboarded their first AM system in 2011, a Polyjet technology from Stratasys. As its learning curve progressed, they enhanced their development application portfolio with a wide range of AM processes that followed a typical progression through FDM, SLS and then metal AM technologies.
Using more than seven different AM process modalities for multiple applications today, GA-ASI continues to invest in several elements essential to the growth of their AM landscape to serve GA-ASI’s products and customers. Specifically, GA-ASI has invested a lot of resources in facilities infrastructures, in a rapidly growing team of Subject Matter Experts (SMEs), in AM equipment as well as in R&D in order to reduce risks at multiple levels related to materials, processes and applications.
This means, for instance that, for rapid prototyping purposes (non-flight), GA-ASI have developed multiple resources internally, including the AM group supporting engineering that leverages most of the AM technologies, whereas for manufacturing operations of flight-ready product development and production parts, FDM, SLS, metal-LPBF, DED-W, BJT and LSAM/BAAM will be more indicated. Needless to say that these technologies are supplemented by engineering design (DfAM) capabilities, post-processing equipment, material conditioning and testing, inspection or metrology infrastructures.
“With nearly 7,000+ parts 3D printed per year, we have over 320 different SKUs that are flying today across several of our aircraft platforms, representing over 300,000 accumulated flying hours. That represents a mix of polymer, composite, and metal parts. The military RPA market, with its high mix, low volume model, is a perfect area of the aviation industry to introduce AM. Back in 2011, we started building up our infrastructures and brought in our first printers, etc. Back then, it was mainly for prototyping applications to help us explore the materials and the potential areas for its applications on our products. In 2016/2017, GA-ASI leadership recognized the value and need to build a team of AM SMEs, and in 2018, a formal department was created. We started with only four people, and now, we have 14 people dedicated to AM technologies. One of our main areas of focus was to develop the structure of our strategic roadmap composed of an AM technology ecosystem to help us transition from prototyping to a production-ready operation and help drive its implementation across the organization in order to go after multiple applications. Thermwood’s LSAM is just one of the technologies that enables us to achieve that goal,” Fournier recounts.
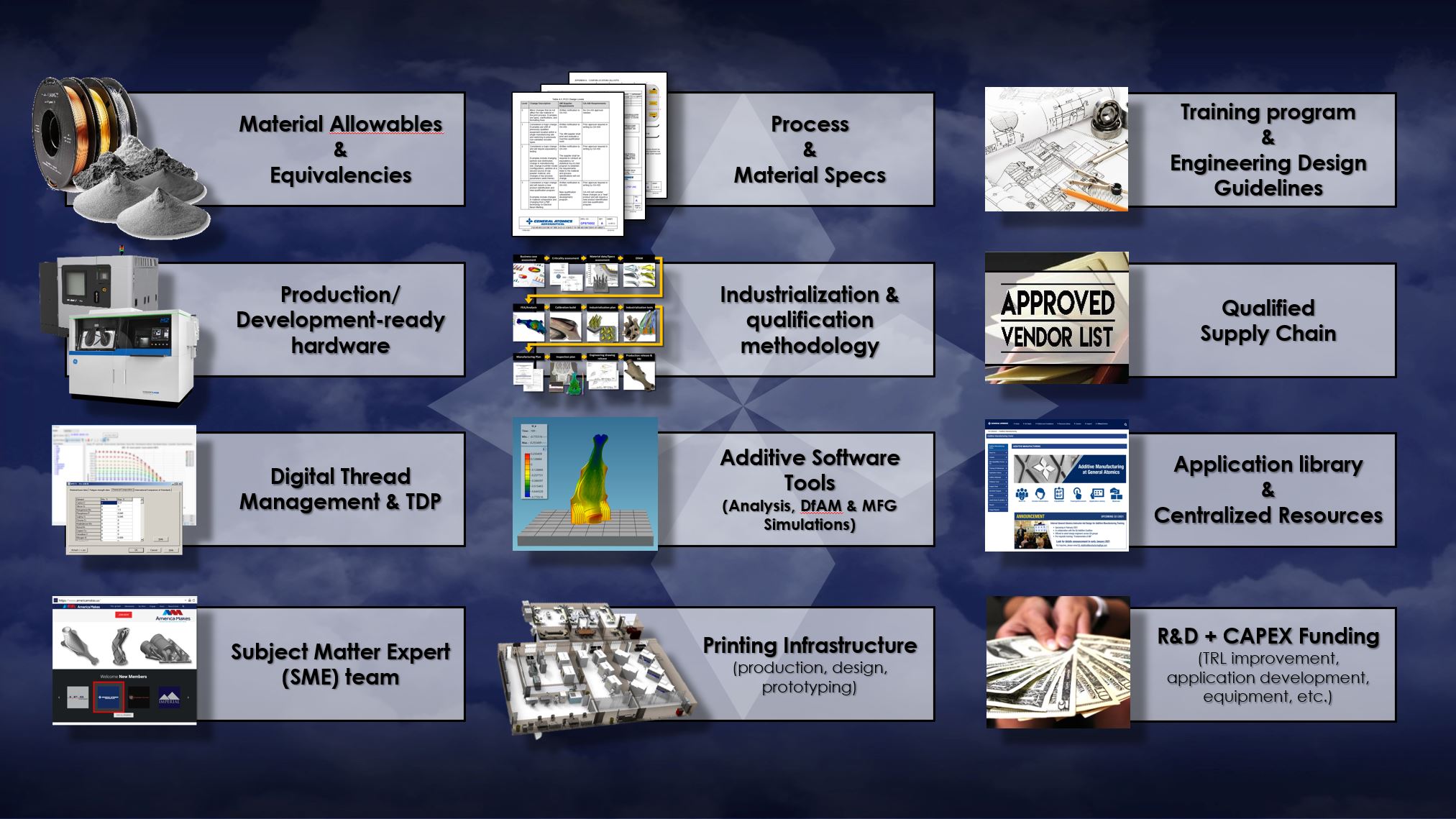
After building a solid AM team and strategy foundation, GA-ASI then opened the company’s Additive Design and Manufacturing Center of Excellence (AD&M CoE) in 2021. The Center focuses on rapid-reaction manufacturing serving GA-ASI’s line of Unmanned Aircraft Systems (UAS) using fully functional and flight-ready Additive Manufacturing (AM) applications. In addition, they support research and development for applied risk reduction purposes related to large-scale tooling, existing and next-generation flight hardware.
While GA-ASI conducts a wide range of recurring production activities at its AD&M CoE, Fournier outlines the fact that the demand for in-house rapid-reaction and low-rate manufacturing for early phase lifecycle development programs has required them to rely on a strong AM manufacturing supply chain for the overflow production of complex end-use thermoplastics and metal parts.
Speaking of the purposes these infrastructures serve through their 8,500 square feet (790 m²) Center of Excellence, Fournier explains:
“We leverage rapid manufacturing capabilities to respond to low to medium volume requests on metal, composite and thermoplastic fully functional parts (form, fit and function). There is a distinction between prototyping and rapid manufacturing in the depth of qualification efforts required for the two different type of use of AM. The latter requires qualifying the materials, the technology and reducing all application-related risks through engineering substantiation.
The second area of interest is R&D. We invest in materials and processes to qualify applications for each AM technology of interest. For instance, over the past several years, we invested significant R&D resources to qualify tooling applications using Large Scale Additive Manufacturing (LSAM) technology, which is now part of our production portfolio. The R&D is really application-based and we keep a close look at the near-to-medium term return on investments (ROI).
The third aspect of our work is about recurring production. We do build plastic and metal parts that go directly onto aircraft after an extensive quality assurance process. We keep between 15% to 30% of our production demand in-house to maintain our production-level processes and skills, and we leverage our qualified contract manufacturers for our overflow production needs. And that outsourced production keeps increasing. Our main goal is to achieve rapid-reaction manufacturing using multiple AM technologies, bring applications from a “one-off” to a recurring level, and fortify our supply chain to support our fast AM growth.”
A portfolio of applications enabled by AM
While our interest in GA-ASI’s adoption of AM has been raised on the heels of a use case achieved with Thermwood’s LSAM technology, our conversation with the company’s representative reveals how they have developed several families of applications with AM technologies.These families of applications include for instance: conformal structures, air management ducting and manifolds, covers and panels, engine and exhaust components, mill fixtures, ultralight structures, lamination tools, OML components and heat exchangers. These are just a few examples we kept from our conversation with Fournier. Many more are being explored right now.
No matter what the application is, the team at GA-ASI always kept in mind three things:
- It’s of paramount importance to ensure a valid business case before “going all technical” (“printing because we should, not because we can”);
- The intended manufacturing goals (is it for prototyping or production purpose? It’s crucial to differentiate between these two goals as they will require different qualification efforts);
- And the technical requirements which drive the choices of the right combination material, process and design approach.
The case of the lamination mill fixture production achieved in collaboration with Thermwood
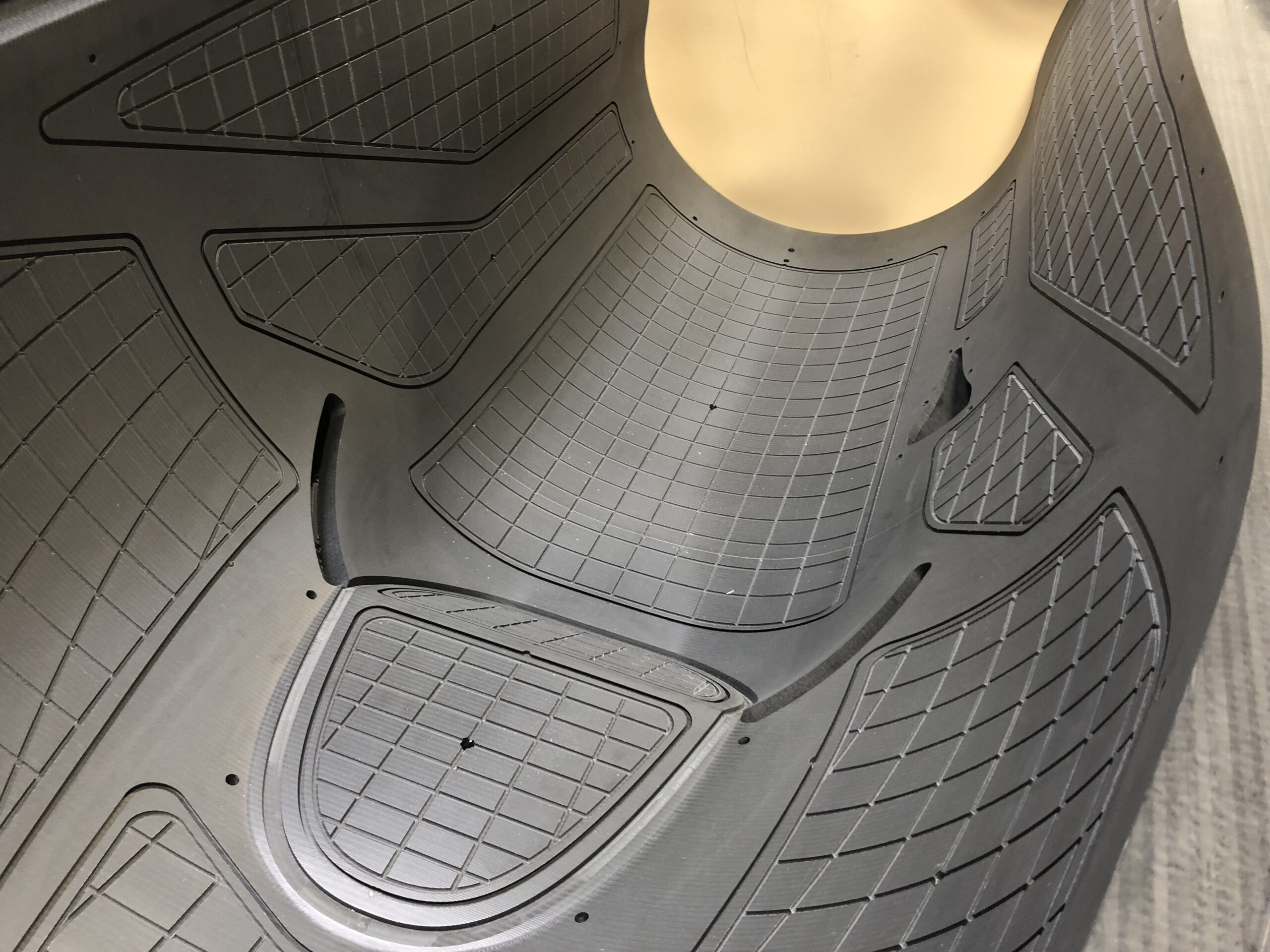
If you’re a regular reader of 3D ADEPT Media, you probably know that Thermwood is one of the rare companies providing very large format 3D printing hardware and services with composite chopped Fiber Reinforced Polymer (FPR) pellet materials. With an increasing portfolio of machines, the company partners with a wide range of material producers, industrials in vertical industries adopting AM and academics to explore applications that could lead to viable business cases for its Large Scale Additive Manufacturing (LSAM) technology.
Speaking of the CNC trim tool/fixture, Scott Vaal, LSAM Product Manager at Thermwood, explains that it “is typically used to hold a 3 dimensionally formed plastic or carbon fiber composite part for secondary trimming operations such as final perimeter shape and holes and cut-outs. Parts are commonly held to the fixture using vacuum or a combination of vacuum and other mechanical holds down”. “Several traditional methods [are often] used to make CNC trim tools/fixtures, from gluing up blocks of various materials and machining it to shape, pouring a cast type material on the back side of one of the untrimmed parts, and metal or even wooden support structures used by themselves or in conjunction with the poured or glued up blocks method,” he adds.
According to Fournier, the development of a lamination mill fixture tool using AM processes originally came from the fact that they wanted to explore the technical feasibility of making such a tool cheaper and faster:
“We started in 2017/2018 by selecting a couple of R&D projects related to this type of tool (room temperature lamination fixtures). The main challenge at the time was to find a toolmaker who had the technology to explore the application. Although we initially started by working directly with Thermwood application team, we started soon thereafter working and qualifying toolmakers who are using Thermwood’s technology.”
Given the price of the 3D printer, it was risky for GA-ASI to start by investing in a technology with no certainty that it would deliver on the business cases they wanted to build. Not to mention that, once you get the 3D printer, you need to have a qualified workforce that could operate the machine, all the pre- and post-processing equipment that could help deliver the desired part, as well as the right facilities to host this type of large-size equipment.
“Given all that, it becomes pretty capital-intensive for most companies to get into this technology. That’s why our strategy was not to buy a printer right away but rather to develop our supply chain partners. Developing and qualifying the application helped us to create the “demand signal” for the applications that could be met by potentially insourcing this technology at a significant infrastructure and resource cost. After convincing ourselves that the technical requirements could be met for the mill fixture tooling applications, we have since expanded our usage of LSAM technology beyond the tooling use cases, and are continuing our investment into our supply chain,” Fournier explains.
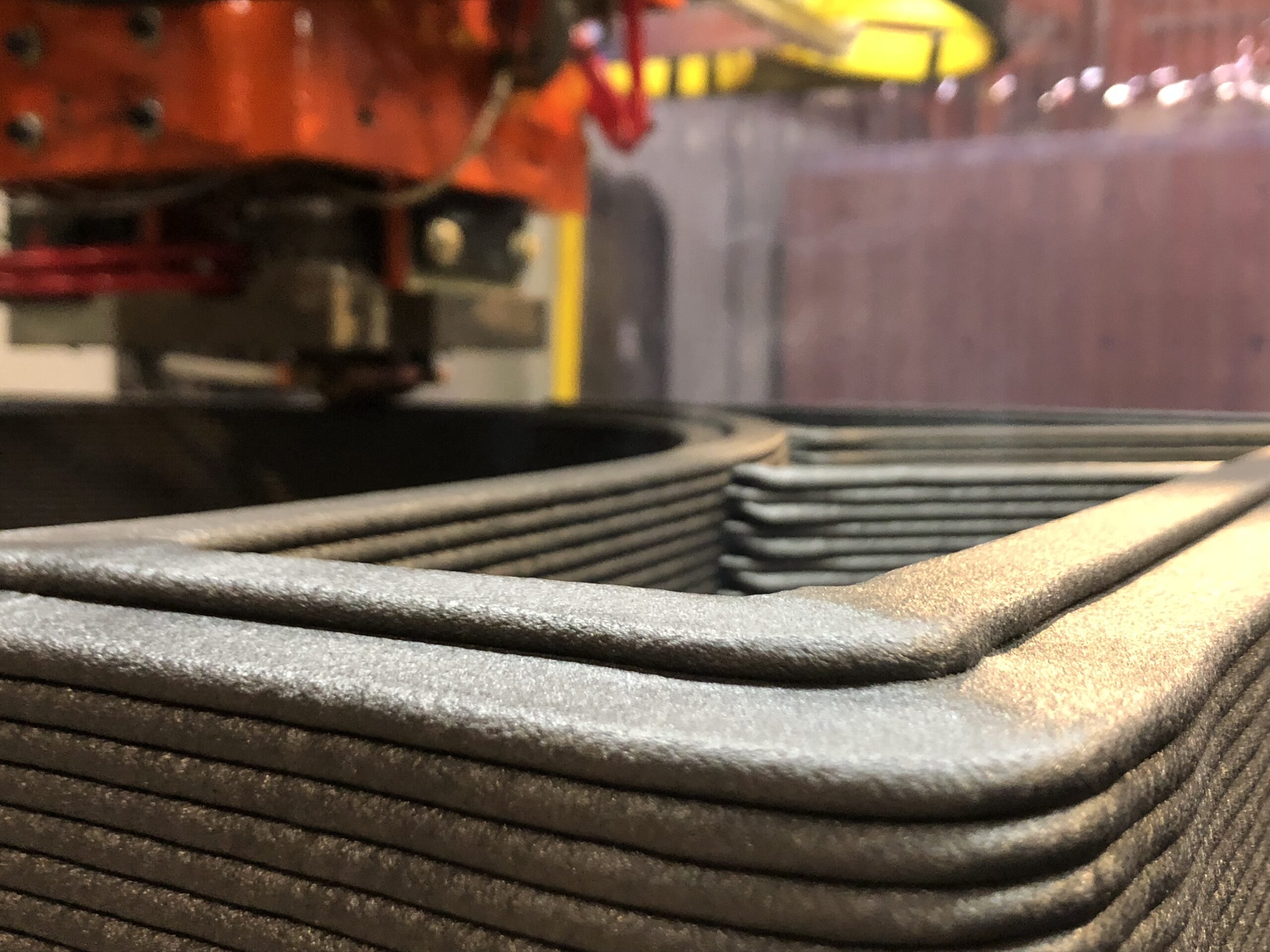
The exploration period for this business case took about 2-3 years. It was marked by a lot of testing and manufacturing trials before they concluded it was a viable tool for production. The 3D printing process itself of the mill fixture took about 16 hours and required the use of a Thermwood LSAM 1200 which processed an ABS material (20% Carbon Fiber filled). The post-machining process of the critical tool surfaces took significantly longer. Overall, the process delivered a final tool that weighs 1190 lbs (540 kg).
“The LSAM is available in many models, sizes, and configurations to fit a variety of needs. Each LSAM is equipped with the same unique and patented Melt Core system which can process and print a wide variety of materials that can be used for room temperature applications all the way up to high temperature materials that can be used for aerospace autoclave tooling that must exceed 350 degrees Fahrenheit [177 °C]. To date, we are unaware of a practical material that the LSAM cannot process and print”, Vaal reminds us before commenting on the production: “this part was pretty straightforward on the printing side of things and lent itself very well to the process. The only real challenge was on the 5-axis CNC router side of things. There was not enough router head clearance to be able to machine some seal groves on an approximately 2” wide flange on one end of the part. So, we ended up splitting and printing the flange section separately so we could machine the flange and groves easily and then bond it to the main section accurately using dowel pin locating holes to finish the part.”
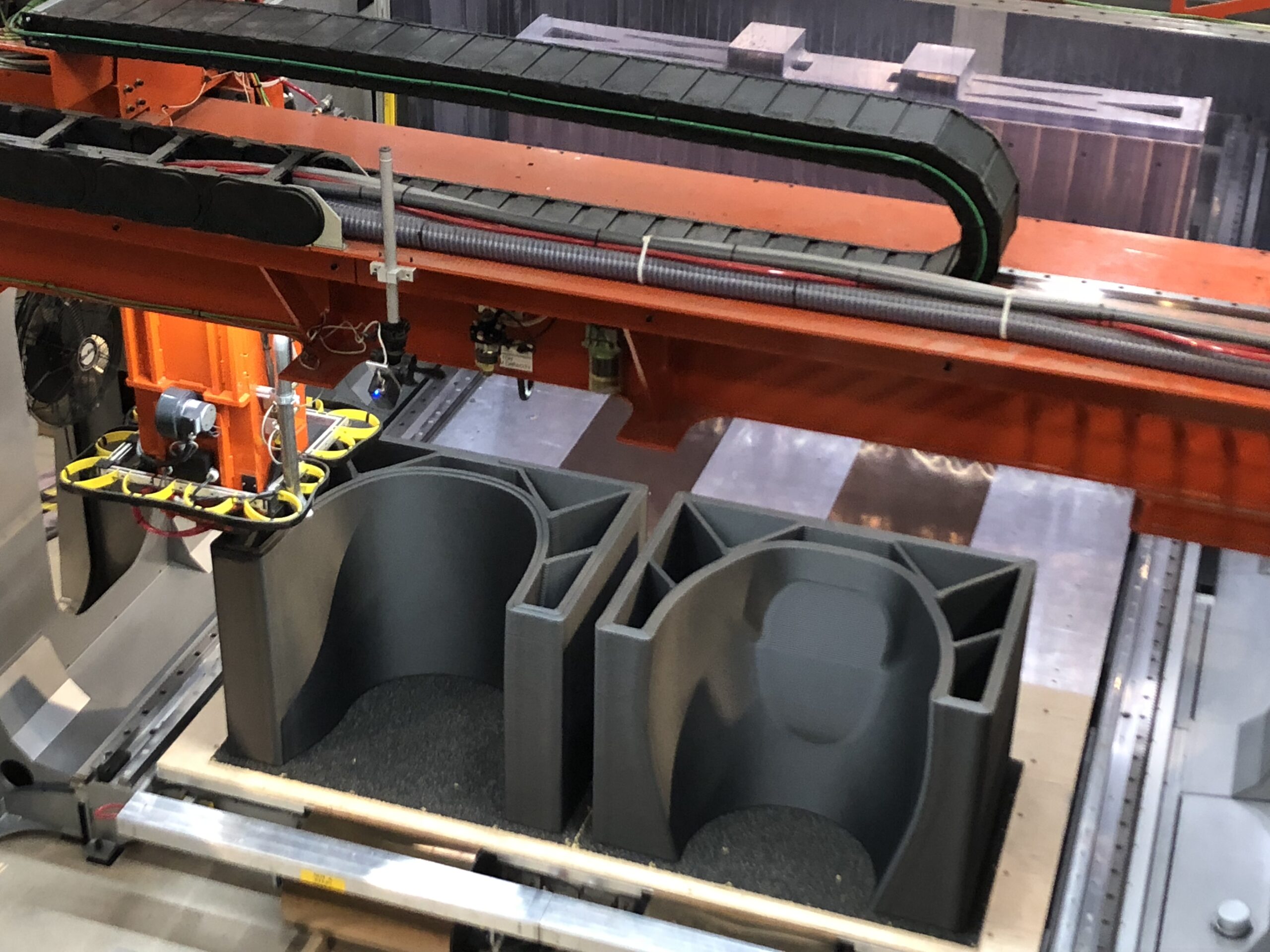
Interestingly, this application is said to have enabled GA-ASI to save costs of around $50 000 (€46,192) vs traditional methods.
Calculating these cost savings can be quite simple nowadays: “for tooling applications for instance, one can get quotes from multiple vendors of both conventional and additive options, and make the comparison from there. The design aspect of the work can sometimes be a significant difference in the quoting process however. Over time, you accumulate enough statistics on multiple tools geometries to start getting a metric of cost per tool face sheet surface area. This is a typical metric used in the tooling industry. It is important to note that these business cases can differ wildly depending on tool geometries. Not all tools are best suited for LSAM technology. Machine manufacturers on the other hand have a different way of calculation because they need to take into account the depreciation of the machine, the staff required, the materials, etc. but they essentially come down to a dollar per pound or square footage,” Fournier outlines.
Fast forward to today: going beyond mill fixtures with Thermwood’s LSAM
Today, GA-ASI has grown a cross-functional team of subject matter experts on the technology within multiple engineering, quality, procurement and manufacturing functions, and they continue to invest in this technology in order to reduce additional technical and business challenges encountered as they push further the application space for this technology.
“Today, we are doing both tooling for large room temperature mill fixtures, exploring higher temperature applications, and also some end-use parts for very large structures. Each application comes with its share of challenges,” Fournier emphasizes.
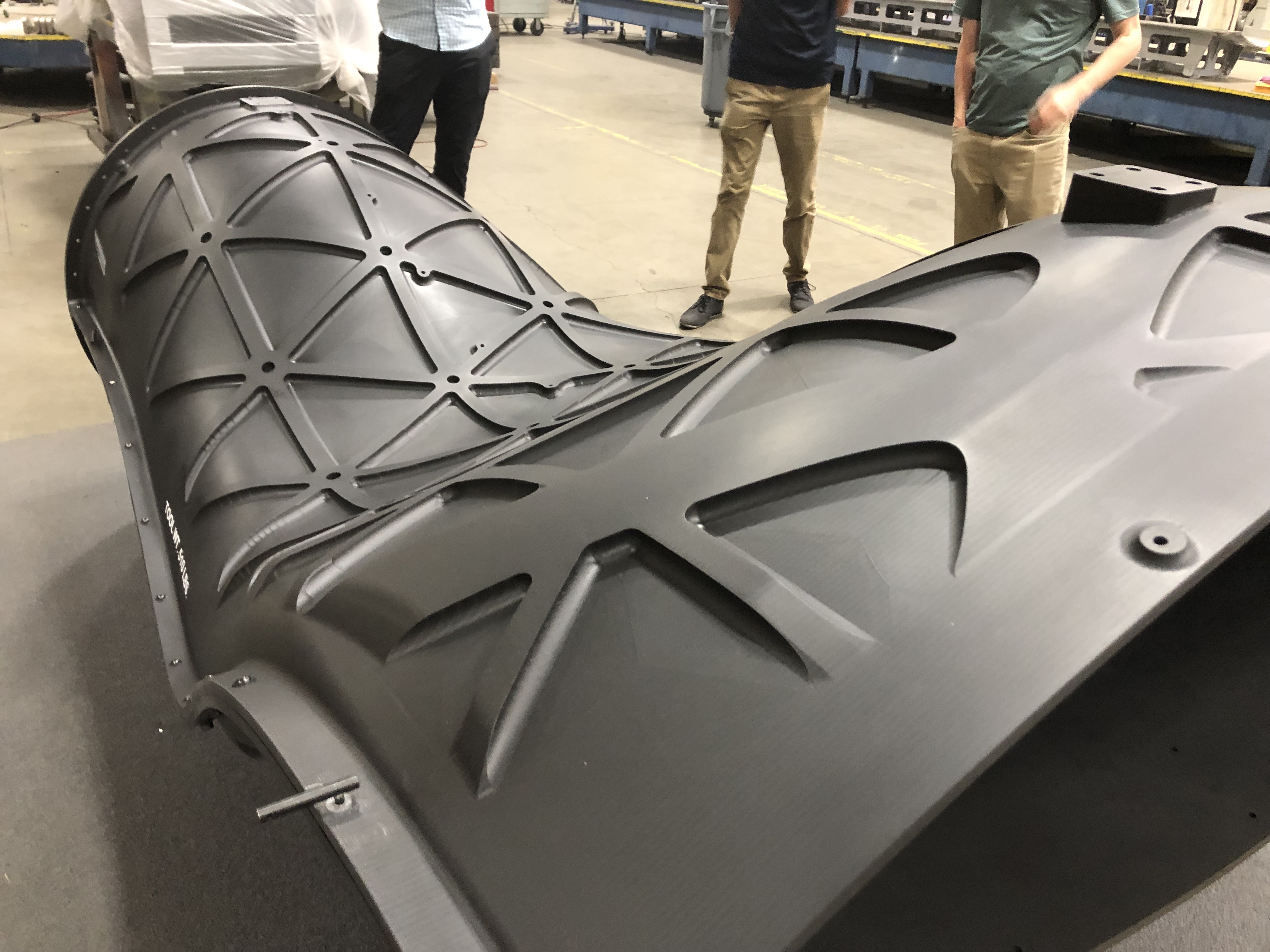
“We are also pushing our exploration towards the higher temperature side, with lamination tool. For such applications, one of the very significant and limiting challenges of this technology is the CTE”, he notes. [Coefficient of Thermal Expansion = describes how the size of an object changes with a temperature change. In other terms, the material property is indicative of the extent to which a material expands upon heating.] Put simply, and without digging too much into technical details, the anisotropic nature of the printed material properties creates lamination application issues. For instance, the thermal expansion along axis XY plane is very different from the one measured along the Z axis. This leads to potentially significant lamination issues on tool and part integrity, depending on the temperature ranges and tool face geometries.
“Because of the anisotropic properties, for some lamination tool geometries, the LSAM technology brings significant challenges in the tool design to pre-compensate and control the tool shape during thermal cycling, as well as for the demolding process which can impact the laminate part integrity itself. In the end, the technical risks MUST be balanced with the benefits brought by the manufacturing technology used. This particular technology is good and beneficial for room temperature applications. Even at room temperature, the application space is limited to a certain class of tool geometries and end use structures. With the partnership of our supply chain partners, we are now pushing the boundaries of the application space to see what can be beneficial– from a business standpoint”, he completes.
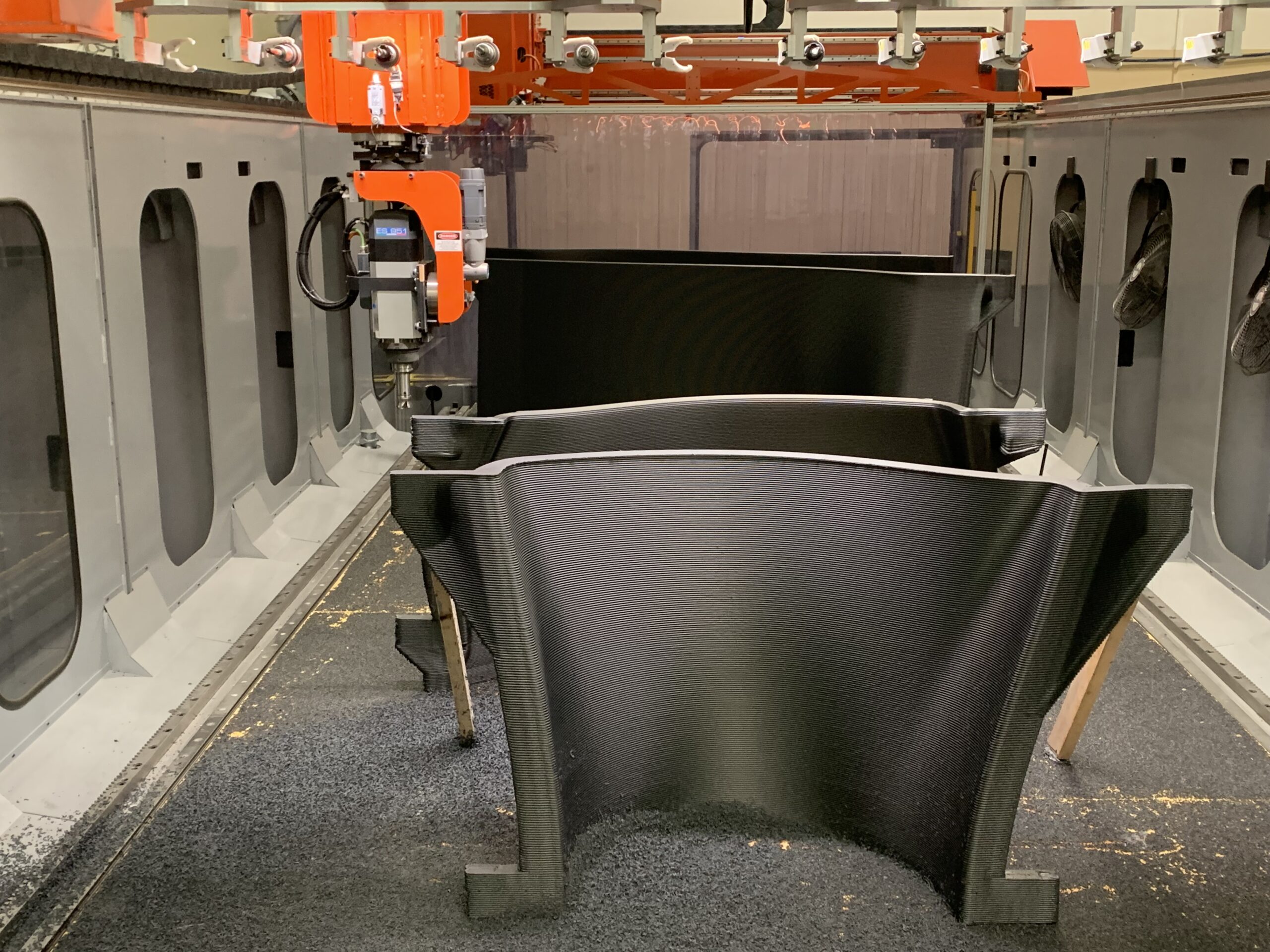
The journey continues
The implementation of AM technologies within the aviation and defense industry is a long journey that continues “one application at the time.” Through his 15 years of experience with AM, Fournier shared a few of his learning:
- Each industry, and each user within a given industry have specific application sets, and it is important/critical to identify the business benefits at the aggregate level to help motivate the investment of capital and resources to bring AM to the level where those benefits can be realized
- Many AM technologies have reached an industrial level and can be used for production-ready applications with proper and sufficient controls. Others require further establishment of AM ecosystem elements such as standards and better equipment engineering. But AM should not be the end goal. AM is a powerful enabling tool in a large toolbox which it combined with conventional technologies as well. The key to success is to find the right applications for AM.
- It was beneficial to GA-ASI to invest in building a team of SMEs ahead of investing in infrastructure and equipment to build a strong roadmap AM ecosystem and establish its value propositions.
- AM use cases can be summarized in order of growing value proposition by a) part substitution to achieve component-level benefits b) part consolidation to avoid assemblies and associated costs implications, leading to c) novel and uniquely enabled design for AM (DfAM) solutions, which may rise to the sub-system level. As well, sustainment solutions are not to be underestimated in the later phase of our product lifecycles.
“Typically, I describe AM as a “luxury car” technology analogy… When we consider new applications for AM, we always ask ourselves: why AM? Using a “luxury car-level technology” requires finding an equivalent high level application and benefits. This means for us at GA-ASI more parts integration, even better performance designs, and manufacturing cost reduction. Achieving that generally will require creating new more complex designs that conventional manufacturing processes will increase in cost and tooling requirements, whereas AM will be able to handle such complex design with little-to-no cost difference, and often, without the need of any tooling. It’s about using AM for the good reasons,” Fournier concludes.
GA-ASI has already been able to save millions of dollars in non-recurring tooling and save very significant recurring cost on their aircraft platforms. As they continue pushing the boundaries of the applicability of various AM technologies and exploring new applications, they anticipate being able to achieve more parts integration, and over time, increase the % of AM content on their aircraft platforms from <1% up to 75% depending on the class of aircraft and its survivability level, avoid tooling when possible in the manufacturing process of their components, as well as helping to bring novel AM tooling solutions when required.
This article has initially been published in the 2023 January/February edition of 3D ADEPT Mag.